2022/10/03
『粉体ハンドリング設備計画の基本的な進め方』
Basic procedure for powder handling equipment planning
1. 必要な条件を明確にする
粉体の単位操作を主単位操作と副単位操作に分けて検討する。主単位操作、副単位操作とは、製品を作るため粉体に何らかの加工を加える操作を主単位操作、主単位操作をするために行う操作を副単位操作という。副単位操作、すなわち、粉体の受入、貯蔵、貯蔵から切り出し、輸送、計量、集塵、包装などの操作を行う設備を粉体ハンドリング設備
(図1.)と呼ぶ。
表⒈は、計画を進めるときに明確にする必要がある条件の例である。
表⒈粉体ハンドリング計画に必要な条件の例
工程 | 単位操作 | 計画にあたって明確にするべき条件 | ||
---|---|---|---|---|
主単位操作 | 副単位操作 | |||
前工程 |
処理量レイアウト 単位操作毎に配置を検討する →屋内、屋外 →広さ、高さ ユーティリティ →電源、空気源、清水源 雰囲気 →温度、湿度 →危険・安全 材質 →接粉部、その他 粉体物性 →流動性指数(注記1.) 安息角 圧縮度、密充填、粗充填 動的かさ密度(注記2.) スパチュラ角、凝集度、均一度 →噴流性指数 崩壊角、差角、分散度 粒度、付着性、腐食性、爆発性、毒性 量と時間の問題 →量:少量、多量 →時間:短時間、長時間 その他取扱い上の注意 |
|||
粉砕 分級 造粒 表面改質 混合 混練 溶解 乾燥 反応 焼成 |
貯蔵 切り出し 輸送 集塵 計量 包装 |
受入方法 貯蔵日数→容量 輸送時間 →輸送能力・経路・距離 量、精度、時間 排出方法 →連続か、バッチか →一括か、漸次排出か 各単位操作における ① タイムサイクル (必要時間) ② 現象 固まる、溶ける 造粒する、粉砕する 発熱する、吸熱する 加熱する、冷却する 吸湿する、乾燥する |
||
後工程 |
注記1.圧縮度C:C=100(P-A)/P %
注記2.動的かさ密度W:W=A+(P-A)・C/100
P:密充填、A:粗充填
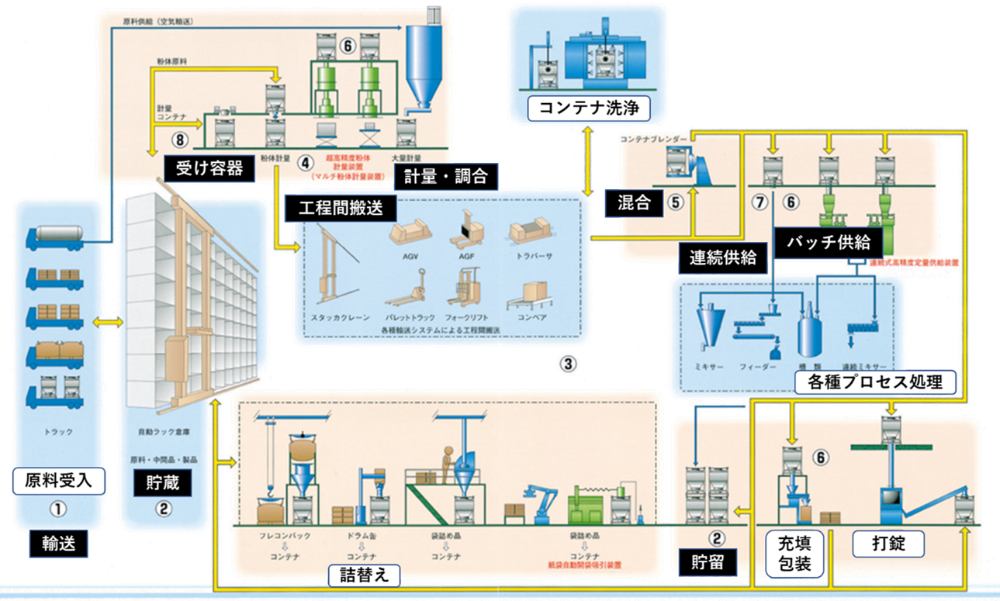
図1. 粉体ハンドリングシステムの設備フロー例 (出典先:赤城エンジニアリングHP)
① 原料の受入:荷姿、容量、数、受入方法
紙袋(人力開袋、自動開袋機、空袋処理)
フレキシブルコンテナ(人力取出し、自動取出し)
コンテナ(人力開口、自動開口)
タンクローリ(空気輸送、機械的輸送)
② 貯蔵:容量、設置場所、貯蔵からの切出し方法
③ 輸送:輸送量、距離、レイアウト、コンタミの可否、受取場所の数、輸送先の数
機械的輸送(形式)
空気輸送(圧送・吸引、低濃度・高濃度、高速・低速)
④ 計量:(量、精度、時間、供給方法)
バッチ供給か連続供給か。バッチ供給の場合、短時間で一括供給してよいか、ゆっくり漸次供給する必要があるか
バッチ精度の場合、計量値に対する精度か、フルスケールに対する精度か
連続精度の場合、瞬時精度か、1分間精度などのある時間での精度か
⑤ 操作をした結果どのような現象が起こるか:
固まる⇔溶ける
発熱する⇔吸熱する
吸湿する⇔乾燥する
など
⑥ 設備レイアウト:
屋内・屋外
広さ、高さ
⑦ ユーティリティ:
電源、空気源、清水源
⑧ 周囲の条件:
雰囲気(温度、湿気、危険・安全)
⑨ 材質:
接粉部
その他
⑩ 粉体物性:
流動性指数(安息角、圧縮度、密充填、粗充填、動的嵩密度、スパチュラ角、凝集度、均一度),
噴流性指数(崩壊角、差角、分散性、粒度、付着性、腐食性、爆発性、毒性)
各単位操作を計画するときに行う必要がある検討項目の例と、調べておく必要がある粉体物性の例を 表⒉に示す。 表⒊は、特に貯槽の計画に絞って列挙している。
表2.粉体物性の例一覧
単位操作 | 検討項目例 | 検討に必要な粉体特性 | その他の条件 |
---|---|---|---|
粉砕 | ボールミルの粉砕動力 | 原料80%パスの粒径、粉砕物の80%パスの粒径 | 粉砕仕事指数 |
粉砕に要するエネルギ | 砕料(原料)の比表面積と砕成物の比表面積又は砕料の粒径と砕成物の粒径、砕料の真密度、ポアソン比、ヤング率、圧縮強度、引張強度、曲げ強度、せん断強度 | 粉砕抵抗、粉砕能 | |
分級 | 篩分け装置の能力 (Gluckの推定法) |
ハーフサイズの%、オーバーサイズの%、かさ密度、湿分 | スクリーン目開き、篩分け効率、篩分け装置の段数、傾斜 |
篩分け装置の能力 (網上粒子層厚法) |
粒子径、粒子かさ密度 | 網面上の粒子移送速度、網面上の粒子層の厚み、網面の幅 | |
サイクロンの分離粒子径 | 粒子の真密度 | 流体の密度、入口面積、外筒の半径、内筒の半径、入口速度 | |
サイクロンの圧力損失 | 空気の密度、入口面積、外筒の直径、内筒の直径、外筒部の長さ、円錐部の長さ、入口速度 | ||
造粒 | 皿型造粒装置のホールドアップ、滞留時間、動力 | かさ密度、内部摩擦角 | パンの直径、高さ、傾斜角、回転数 |
混合 | V型ミキサの動力 | かさ密度、安息角、壁面摩擦係数 | 回転数、回転半径、投入率 |
横型リボンミキサの動力 | かさ密度、内部摩擦係数 | 挿入率、リボン径、リボン長さ、回転数 | |
乾燥 | 乾燥機の能力 | 乾物の比熱、乾燥前の含水率、乾燥後の含水率、乾燥前の材料温度、乾燥後の材料温度 | 水の比熱、湿球温度、熱源温度、伝熱面積や乾燥機容積 |
貯蔵 | 貯蔵容量、容積 | 安息角、かさ密度 | 容器寸法、ホッパ半頂角 |
形状 | 壁面摩擦角、有効摩擦角 | ||
板厚、架橋の強度 | かさ密度、壁面摩擦角、内部摩擦角 | ||
材質 | 腐食性等の化学的性質 | 温度、雰囲気 | |
供給 | 振動式供給機の能力 | かさ密度、粒子径、水分 | トラフの幅、粉体層の厚み、トラフの傾斜、振幅、振動強度、輸送速度(振幅、振動強度、角速度、振動の方向) |
マス式テーブルフィーダの能力 | かさ密度 | マスの容積、マスの数、回転数 | |
スクリュフィーダの能力 | かさ密度、安息角、スクリュシャフト及び羽根との壁面摩擦係数、ケーシングとの壁面摩擦係数、内部摩擦角 | スクリュ外径、スクリュシャフト径、スクリュピッチ、回転数 | |
輸送 | ベルトコンベヤの能力 | 最大粒径、平均粒径、かさ密度、安息角 | ベルト幅、ベルト速度、ベルトの傾斜角度 |
低濃度高速空気輸送の圧力損失 | 粒子径、粒子の形状、見掛け粒子密度、安息角 | 輸送量、配管径、配管長(ベンド数、分岐数等を含めた相当長さ)、垂直方向距離、空気量、空気の粘土、空気の密度、空気と配管の摩擦係数 | |
集塵 | 重力集塵装置の分離粒子径 | 粒子かさ密度 | ガス密度、ガスの粘度、水平に流れるガスの流速、落下させる距離、沈降室の奥行き |
電気集塵機の集塵率 | 粒子径、見掛け電気抵抗率 | 集塵空間の電界強度、処理ガス量、処理ガス速度、ガスの粘度、温度、圧力、極間距離(平板型)、管形集塵極の直径(管型) | |
バグフィルタのろ過面積 | 粒子径 | 粉体濃度、圧力条件、処理風量、空気温度 |
表3.貯蔵における計画に絞った粉体物性の例
検討項目例 | 検討に必要な粉体特性 | その他の条件、対策 | |
---|---|---|---|
容積の決定 | かさ密度(まばら充填)、安息角 |
要求仕様: 貯蔵日数、使用量 |
|
形状設計 | マスフロー設計 | 壁面摩擦角、内部摩擦角 | ・貯槽の形状(円形、角形) ・寸法(直胴部高さ、ホッパ部高さ、出口寸法) ・ホッパ半頂角 |
閉塞限界径 | 壁面摩擦角、内部摩擦角 | ||
流動性の 判断 |
流動性を計測する方法の例 ・容器からの排出時間 ・壁摩擦角 ・Flow Index(単純崩壊応力、かさ密度、粒子かさ密度、空間率) ・Carr法(安息角、圧縮度、スパチュラ角、均一度又は凝集度) |
||
板厚設計 | 貯槽壁にかかる粉体圧 | 壁面摩擦角、内部摩擦角 かさ密度(密充填) |
|
接粉部材質 | 腐食性等の化学的性質 | 耐食性材料の選定 | |
付着性 | 材質の選定、研磨、ライニング等の付着力減少対策 | ||
摩擦性 | 耐摩擦材料の選定 | ||
貯留方法 | 腐敗 | 温度、湿度、時間 | |
吸湿性(平衡水分、吸湿速度) | 湿度(絶対湿度、相対湿度) | ||
乾燥性(平衡水分、乾燥速度) | 温度差による水分の移動・結露 | ||
固結性、凝集性 | 湿度、粉体圧等 | ||
ハンドリング方法 | 噴流の有無 | Carr法(流動性、崩壊角、差角、分散度) | 搬出装置のシール性能 |
偏析の有無 | 粒度分布、粒子形状、粒子かさ密度 | – | |
粉砕の有無 | 粒子形状、硬さ、強さ | – | |
毒性の有無 | 化学成分 | – | |
発塵性 | 粒子径、粒子かさ密度 | – | |
帯電性 | 電気的特性 | アース、イオン放射、接触材料の種類、湿度 |
⑪ 量と時間の問題:
同じ粉体を同じ種類の操作を行うときでも、量が多い時と少ないときは、ハンドリングの方法を変えなくてはならないときがある。たとえば、貯槽においては少量のときは問題がなくても多量のときはブリッジが発生して排出不能になることがある。計量においては、多量のときの精度に問題がなくても、少量になると付着や発塵による誤差が問題になることがある
貯留時間が長くなると、圧密、吸湿、固着、変質などのトラブルを起こす粉体があるので注意が必要である
2. 使用できる設備を列挙し、適か不適かを検討する
設備の検討例を表⒋に示す。この設備は、食品製造プラント事例である。輸送装置は、レイアウトが自由にてき、粉溜りが少なく、コンパクトな空気輸送装置を採用した。
表4.設備の検討例一覧
設備検討 | 受入方法 | ||
---|---|---|---|
タンクローリ | コンテナバック | 紙袋 | |
粉体名 | A粉/B粉 | C粉 (500kg/バッグ) |
D粉~K粉 (25kg/袋) |
受入 | 空気輸送 | 投入 | 投入 |
貯蔵 | 屋外 サイロタンク |
屋内 サイロタンク |
屋外 サイロタンク |
搬送 |
(1) 空気輸送 低濃度輸送(ロータリバルブ) 高濃度輸送(フロータンク) (2) 機械輸送 スクリュ+バケット+スクリュの組合せ フローコンベヤ |
||
中間 タンク |
使用する 使用しない(処理能力、精度) |
||
計量 |
(1) 実計量方式(投入量計量方式) 排出時間を短時間にできる (2) 排出計量方式 輸送と計量を同時にできる (3) 累積計量方式 計量ポット数を少なくできる |
||
輸送 |
(1) 空気輸送 投入部での固気分離 輸送能力 空気輸送の可否(粉体特性) 輸送方法(原料別に輸送、配合後に一括輸送) (2) ポット輸送 輸送装置(ローラコンベヤ、チェーンコンベヤ、トロリーコンベヤ) 無人搬送車(AGV、AMR、AGF) 輸送方法(原料別に輸送、配合後に一括輸送) |
||
混合機及び 液体タンクへの投入方法 |
(1) 混合機への投入 投入先数 上部受けホッパ(固定式、移動式) 下部受けホッパ(タンブルリフト、反転装置) (2) 溶解槽への投入 投入先数 上部受けホッパ(固定式、移動式) 下部受けホッパ(タンブルリフト、反転装置) (3) ノズルの漏れ防止 溶解濃度 溶解液特性(粘度、析出の有無、変質の有無など) 溶解方法(連続溶解装置、溶解槽) |
- タンクローリで搬入される大量の原料は、空気輸送で屋外サイロに受け入れる。その後、屋内の中間タンクに空気輸送で送り込む。計量指令によって、投入量計量方式で配合計量する。
- コンテナバックで入荷する比較的大量に使う原料は、屋内のサイロに人力で豆乳し、その後、中間タンクに吸引輸送で送り込み、配合計量する。
- 紙袋で入荷した原料は、屋内ストックタンクに自動開袋機または人力で開袋し受け入れる。
- 使用量が少量の場合や、製品によって種類が変わる原料は可搬式の供給装置付ホッパに投入する。配合された原料は、空気輸送装置にタンブルリフトや反転装置を使用して投入する。
- 計量された原料は、空気輸送され後工程に供給する。
3. 設備の選定
図2.は、表⒋で検討し採用した方法で構成した設備例(多品種配合粉体計量システム)である。実際の設備は、後工程の計量粉の送り先が複数あり、サイロの数、受入粉体の種類も多いのだが、基本になる計画方法は同じである。
少量粉計量装置で配合計量された原料は、リフト・反転投入装置で空気輸送装置に投入する。この方法により、天井高さが低い据付場所であったが、多種の粉体の配合計量が可能になった。
後工程への供給は、まず、少量原料を空気輸送し、次に同じ輸送管を使って多量計量粉を送っている。多量粉は、小麦粉や砂糖などの各製品に共通に使用される原料である。
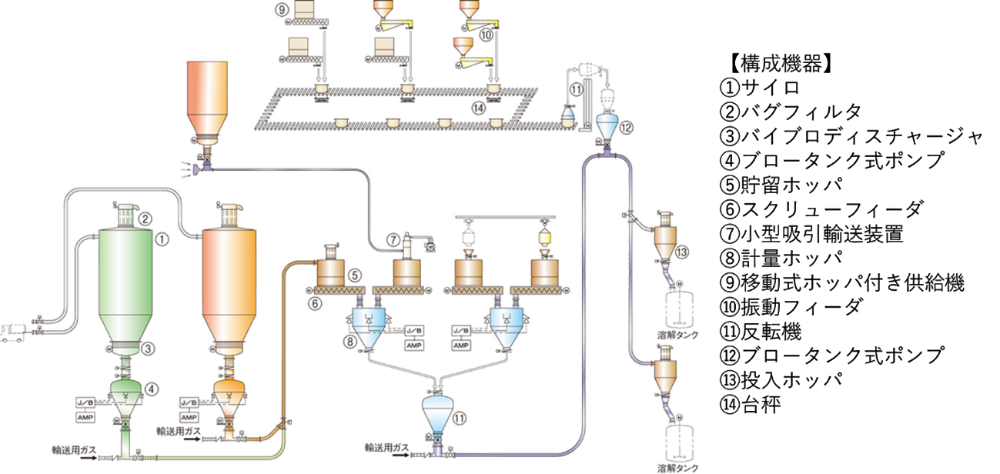
この方法で味材などの少量でも影響を受ける原料の残量を極小にし、コンタミを防いでいる。
以上
【参考文献・引用先】
- 「粉の技術 便利帖」工業調査会 著者:林 恒美
- 「粉粒体ハンドリング技術」一般社団法人 日本粉体工業技術協会 編
-
赤城エンジニアリング株式会社HP
「プラント設備例」: https://www.akatake.co.jp/facility/