2024/07/01
『食品工場の製造工程における金属異物混入防止の考え方』
(後編)
How to prevent metal contamination during the manufacturing process at food factories (Part 2)
前回の技術レポートで取り上げた『食品工場の製造工程における金属異物混入防止の考え方(前編)』に引き続き、本編では、金属異物の管理の考え方、分析方法および異物検出装置について解説する。
1. 食品に混入した金属異物の形状や材質
金属の材質では、鉄やステンレス、アルミニウムが多い。使用されているネジやパーツが緩みなどにより脱落し、混入したと考えられる事例が多い。さらに金属粉も多い。金属粉は製造機器同士の接触による摩耗が主な原因であることが多い。金属粉による健康被害は考えにくいものの、金属粉が食品中の異物として認識されるため問題となる。混入時には、目視や金属検出器で発見しにくいことから、管理が難しい異物である。
2. 食品製造工程で管理すべき金属異物のサイズ
健康被害を考えると限りなく小さなサイズの方が良いが、反面、管理・除去できるサイズにも限界がある。以下に、国内外の基準を述べる。
- 日本・・・食品衛生法第6条「人の健康を損なうおそれがあるものの販売等を禁止」とあるが、種類や大きさなどの具体的な基準はない。
- 韓国・・・食品衛生法にて「長さ2.0mm以上の異物が検出されてはいけない」としている。
- 米国・・・FDA(米国医薬食品局)が食品中の硬く鋭利な異物が含まれていたケース190件の評価を実施し、「最大寸法7mm以下の異物は外傷・重傷の原因にはほとんどならない」と結論づけている。※乳児、手術患者、高齢者などの特別なリスクグループを除く
このように各国の基準は異なるため、食品を輸出する企業は考慮しておくべきである。日本では、管理すべき金属異物のサイズは製造販売元(以下、メーカー)側が決めることが多い。その決定の考え方と、メリット・デメリットを表1にまとめた。
表1. 金属異物管理サイズ決定の考え方とメリット・デメリット
考え方 | メリット | デメリット |
---|---|---|
装置が検出できる最小のサイズ | 装置の能力の限界であるため、決定根拠として説得力がある | 製品によってサイズが異なる場合には、管理が煩雑になり、ミスが生じる |
取引先から求められたサイズ | 取引先(納品先)の考え方が反映されているため、顧客要求として分かりやすい | 設置してある装置の能力によっては、厳しい条件になる |
メーカーが、健康被害を想定して独自に決めたサイズ | 全製品、統一のサイズに選定することで、管理を単純化でき、ミスが起こり難い | 製品によっては更に小さなサイズで管理できるため、装置の性能を最大限に活かしていない |
管理する金属のサイズは、メーカーが取引先に混入が無いことを保証するサイズになる。最近では、φ0.1mmの極微細金属を感知できる装置もあるが、生じる被害、製品特性や作業の状況を勘案し、基本的には食品メーカーが決める。
多くの企業では、表1をベースとしながらも管理の煩雑さを嫌い、1~数サイズにまとめて管理している。その場合には、検出感度が低い製品での設定サイズ(大きなサイズ)に合わせることになる。
3. 金属異物の分析方法
金属異物の鑑定結果は、混入の原因究明と対策の情報となる。鑑定の方法と、その結果から得られる情報を述べる。
(1) 検査機器
-
金属の材質を調べるには、エネルギー分散型蛍光X線分析装置(EDX)を用いる。得られた元素の種類と割合から、材質を特定する。食品加工機器に一般的に使用されているステンレスは、鉄にクロムやニッケルなどを含ませた合金であり、その配合率によってSUS304、SUS316などと呼ばれる(JIS記号)。検査機器、機関によってはこの番号まで特定できるので、ステンレスの混入時に原因究明として番号まで知りたいとの要望も多い。
しかし、食品製造機器類に使用されているステンレスは数種類に限られ、至る所に同一材質が使用されている。また同じ番号のものでも、その中にまた種類があることなどから、材質の鑑定結果から由来を特定するのは困難である
(2) 形態観察
-
金属は硬質であるために、混入時の形状を維持していることが多い。したがって、実体顕微鏡による形態観察により、多くの情報が得られる。特徴的な形状、成型面(加工面)があれば、由来の推測がしやすい。例えば、針金は、その形状と擦れた跡から、元が網状のものかが特定できるケースもある。切断面から得られる情報も多い。加工または金属疲労の切断面では形状が異なり、ニッパーなどの工具で切断されたことが分かる場合もある。
これらの情報が得られれば、混入の原因も絞り込みやすい。また鑑定時に、工場側が原因と推測したものの比較検体品があると、由来の特定はしやすい。
4. 異物除去装置
金属異物の発見は目視では限界があるので、異物除去装置が多用されている。異物除去装置には様々な種類がある。装置の特性を理解し、自社製品にあった装置を選択することがもっとも効果的な「取り除く管理」になる。以下に、代表的な異物検出装置について列記する。これらの装置は正しく管理されることで初めて効果が発揮されるため、管理のポイントについても述べる。
(1) ろ過装置
-
液体や粉体の原材料、製品を細かいメッシュに通過させる「ろ過装置」のことであり、通過させる製品の状態に応じていくつかの方式がある。メッシュ(網の目)のサイズで除去できる異物の大きさが変わり、金属以外の異物も除去される。メッシュが細かいものほど小さい異物が除去できる半面、製品を押し出す圧力が必要になる。
また液体製品でも、固形の具材が含まれているもの(例えば、固形物(つぶ)入り果汁飲料)での使用は難しい。そのため、製品の粘性や含まれる具材などによりメッシュのサイズを変えることになる。したがって、製品ごとにメッシュサイズを設定している工場も多い。以下に各装置を解説する。
(1)-1. ストレーナー
-
飲料やタレなどの液体製品加工中に使用されるメッシュのことをストレーナー(図1. 左)と呼ぶ。配管の一部に取り付けるストレーナーは、インラインストレーナーと呼ばれ、液体を通過させることで異物をろ過する。
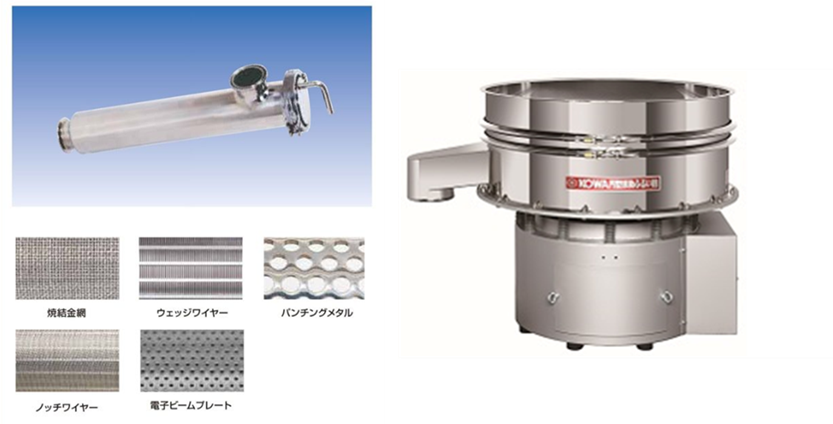
図1. ストレーナー(左)出典:岩井機械工業(株)、篩(右)出典:(株)西村機械製作所
(1)-2. 篩(ふるい)、スクリーン
-
粉体や粒状原料を扱う工場で使用される篩(図1.右)のことで、振動させた篩に原材料や製品を通過させ、異物を取り除く。逆に、豆などの粒径が大きいものでは、豆よりも小さいサイズの篩の上を通過させることにより、小さな異物を篩い落とす。これらのメッシュサイズは40メッシュ、15メッシュなどと表記される。この数値は「1インチ(25.4mm)の1列にある編み目の数」を示し、数値が大きいほど目が細かい。
ただし、同じメッシュサイズでも、使用されている線径の太さよって隙間の大きさが異なる。金網構造のメッシュに加えて、ステンレスに小さな穴をたくさん開けたパンチングタイプもある。
(1)-3. 管理のポイント
-
メッシュに損傷があると異物が確実に除去されないので、メッシュの損傷確認が必要である。装着と取り外し時に確認を行う。製品毎にメッシュサイズを変えている場合、メッシュの誤使用防止が必要である。サイズ表の現場掲示、記録用紙に予めサイズを記載しておくなど、指定サイズを確認しやすいようにしておく。装着時には、メッシュサイズを記入するなど、装着チェック記録を残す。最終工程付近のストレーナーでは、除去異物の確認が必要である。
手前の工程で「入れない」「持ち込まない」ための管理が施されているため、最終工程付近で多くの異物が排除されるのは正常ではない。排除された異物を確認し、由来を特定し、混入を防止する活動を行うことが改善に繋がる。
(2) マグネット
-
金属異物を除去するために、マグネット(図2.)が原材料や製品が通過するラインの一部に組み込まれている装置や、棒状のマグネットを手作業で原材料等にくぐらせる方法がある。マグネットの強さは磁束密度の単位であるT(テスラ)で表記される。日本ではかつてG(ガウス)表記が使用されていたが、1997年より国際的に用いられている単位であるTが使用されている。TとGとは10000G=1Tの関係にある。
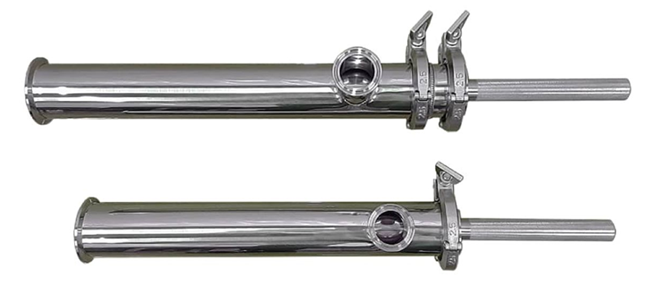
図2. マグネット(配管ライン用)出典:(株)エイシン
(2)-1. 管理のポイント
-
マグネットには永久磁石が使用されているものが多いが、高温にさらされたものなど、使用状況によっては磁力の低下を招く場合がある。重要な工程で用いられている場合には、定期的な頻度(年に1回が一般的)で磁力検査を行い、想定した磁力が保たれているかを確認する。清掃時の金属粉の除去も重要である。付着した金属片を十分に排除しないと、除去した金属が外れて再混入してしまうことが考えられる。
(3) 金属検出機
-
金属検出機(図3.)は、ほとんどの食品メーカーで採用されている一般的な装置である。ただし、この装置を有効に利用するためには、装置の原理を十分に理解する必要がある。
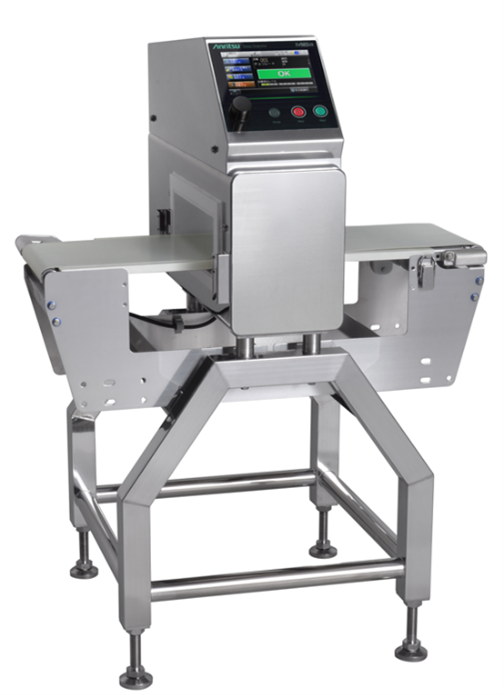
図3. 金属検出機 出典:アンリツ(株)
(3)-1. 原理
-
トンネル状の検出ヘッドの中に製品を通過させ、金属を検出する。検出ヘッドの中は送信コイルと受信コイルによって磁界が形成されており、金属が通過するとトンネル内の磁界が乱れる。この変化を受信コイルが検出することで、金属の有無を感知する。
レトルト食品など包材にアルミが蒸着されている製品は、内部の金属異物の検出精度は低下するか、検出されない。現在ではアルミ箔包装製品用の金属検出機も存在するが、十分に普及していない。
また、製品をダンボールに複数入れた状態で通過させれば検査は早くなる。しかし、製品のサイズが大きくなるほど検出精度が落ちるため、製品はダンボール詰めした状態ではなく、個包装のまま通過させることが多い。
異物の形状による検出精度の差も理解しておく必要がある。針金などの細長い形状の金属は、装置を通過する角度によって金属が磁界から影響を受ける面積が異なるため、磁界を乱す度合いも異なる。したがって、角度によっては検出機を通過してしまうため針金などは要注意である。一方、球状ではどの角度から見ても同じ形状であるため、製品中の混入の向きは検出結果に影響を及ぼさない。
また、食品に含まれる塩分や水分は磁界を乱す原因になるため、異なる食品を同じ条件で検査することはできない。予め製品毎に条件を設定しておき、そこを基準として金属の有無を検出することになる。同じ製品でも塩分濃度にバラつきがある場合(例えば鮭おにぎりの鮭の塩分)には、金属が含まれていると誤検出する。また冷凍食品では通常よりも凍結が不十分な場合、同様に金属が含まれていると誤検出するので注意する。
(3)-2. 金属検出機で検出できるサイズの決定方法
-
製品を通過させる金属検出器のトンネル内では、金属の検出感度は一様ではない。もっとも感度が低いのはトンネルの断面の中央部であり、検出可能な最小のサイズは、この位置で保証されるものである。トンネル内の検出感度の差は、金属検出器の検出ヘッドの種類によっても異なるので、自社で導入している装置の種類・特性について確認しておく必要がある。
機器の特性を踏まえた上で、様々なサイズのテストピースを製品に付着させ、それぞれ複数回通過させる。ここで確実に検出されるもっとも小さなサイズが、その製品で検出できる最小の金属片である。実際には、原材料のバラつきを考慮して、もう1サイズ大きなサイズを採用する場合も検討することが大切である。
(4) X線異物検出機
(4)-1. 原理
-
コンベアで運ばれてくる食品に対して上部からX線を照射し、X線の透過レベルを下のラインセンサで測定する。その測定した信号を解析し、異物の混入を検出する。金属検出機とは原理が異なるため、アルミ蒸着包材製品でも使用が可能である。
また、水分や塩分の影響を受けずに、金属以外の硬質異物も検出することも可能である。ただし、金属だけならば、金属検出器の方が検出精度は高い。また、X線異物検出機(図4.)は導入コストと維持コストともに高額なため、金属検出機ほど普及していない。
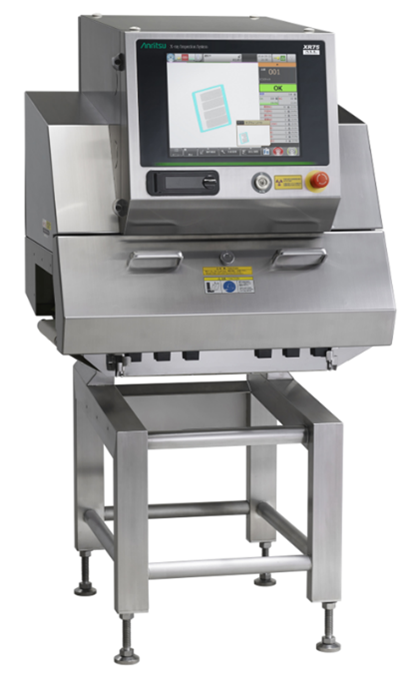
図4. X線異物検出機 出典:アンリツ(株)
(4)-2. 動作確認の方法
-
X線異物検出機用のテストピースは「ガラス」「石」「金属」など種類ごとに存在し、1プレートの中に、大から小までの複数のサイズのピースが入れられている。X線異物検出機の側面には、通過した物質を常時表示するモニターがあり、異物が検出された際には、該当異物が画面上に赤く表示される。動作確認テストでは、1プレート上の複数サイズのテストピースのうち、規定のサイズ以上のものが検出されているかを確認する。
5. 最後に
主な検出装置の原理について解説を行ったが、適切な管理を行わないと、その性能は十分に発揮されない。装置を設置しただけで安心せずに、使用製品や環境にもっとも優れた管理方法を自社の製造工程に導入して構築し、維持管理することが大切である。
以上
【参考引用先】
- 「食品設備・機器事典」編集:食品設備・機器事典編集委員会 発行:産業調査会
- 技術レポート『食品工場の製造工程における金属異物混入防止の考え方(前編)』
木本技術士事務所HP:https://www.kimoto-proeng.com/report/4082 - 岩井機械工業(株) HP:https://www.iwai.co.jp/
- (株)西村機械製作所 HP:https://www.econmw.co.jp/
- (株)エイシン HP:https://www.kk-eishin.co.jp/
- アンリツ(株) HP:https://www.anritsu.com/ja-jp/infivis