2020/03/30
1.基本的な洗浄・殺菌技術
飲料水主にはミネラルウォータの製造は、図⒈熱間充填と無菌充填の製造工程例に示すような流れで行われることが多く、無味、無臭、無色という特性から、次のようなサニテーションをしつかりと行う必要がある。
- 異味、異臭や着色、濁りの防止
- 異物混入(コンタミ)の防止
- 微生物の管理
これらを適切に行うことで安全・安心な製品を供給することが可能になる。したがって、原水、製造設備、工場環境などで汚染が発生しないように、十分な方策を講じることがポイントである。中でも「洗浄と殺菌」は最も重要なプロセスである。
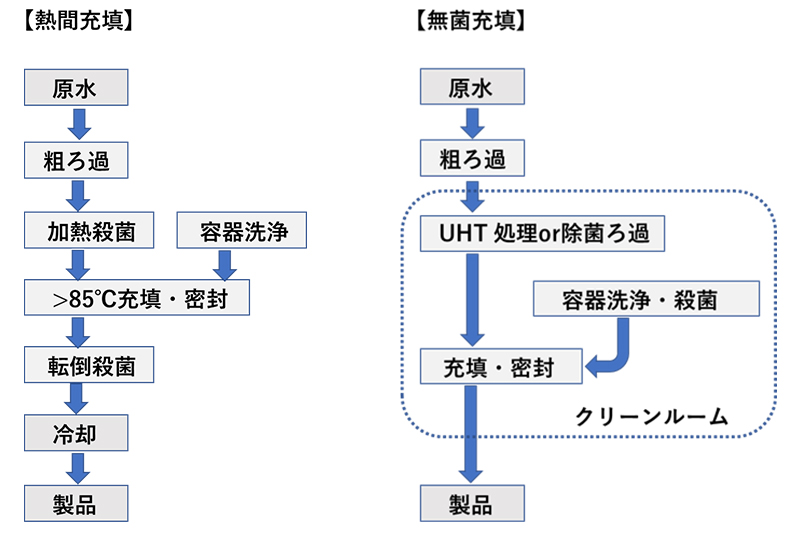
洗浄と殺菌は相互に強く影響を及ぼし合うので、これらを効率よく機能的に実施することが求められる。
洗浄工程は、ラインの汚染を除くとともに微生物の付着量を減らして、殺菌効果を強める働きと、栄養成分を除去することで微生物の増殖を抑える働きがあり、殺菌工程に大きな影響を及ぼす。
また、殺菌が不十分だと堅固な細菌塊(バイオフィルム)がライン中に生成され、洗浄除去できなくなる危険が増す。洗浄と殺菌のコストを少なくするためにも、それぞれの効果を検証し、機能的な洗浄・殺菌システムを構築する必要がある。
一般的なサニテーションは製造終了後、原水タンクから充填機までのライン設備と工場内の床、壁等の洗浄・殺菌を行う。通常、水、温水、水蒸気と洗浄剤、殺菌剤を組み合わせて用いる。翌日の製造まで殺菌剤を飲料水接液部に充満させその状態を保持させる場合もある。室内空間の殺菌も必要で、主に紫外線殺菌灯が利用されている。なお、アセブティック充填ラインでは、よりレベルの高い清浄度が要求され、HEPAやULPAといった高性能エアフィルターが常時稼働するクリーンルームの設置が必要となる。製造前には洗浄剤を十分に除去し、水蒸気や熱水による機器類、配管ラインの殺菌と清浄水での洗浄を行ってから、製造を開始する。
毎日、日常的に実施するサニテーションとは別に一週間ごと、一ヶ月ごとといった年間のサニテーションスケジュールを組み、計画的に設備の洗浄・殺菌を確実に遂行することが重要となる。特に、充填・密封機のように複雑な機械類は、定期的に分解して洗浄、殺菌する必要がある。
飲料水は、接液部に残留した微量成分の影響だけでなく、工場内環境の匂い成分が製品に移香(着香とも言う)することがあり、徹底したサニテーションと環境管理が要求される。
2.製造ラインの洗浄・殺菌
飲料水の製造ラインでは、汚れは少なく、微生物の汚染レベルも低いので、簡単な洗浄・殺菌で十分と思われがちである。しかし、汚染による異味、異臭を防ぎ、微生物や異物の購入がない高品質の製品を安定供給すためには、しっかりとした洗浄・殺菌が必要となる。
①洗浄
洗浄は殺菌の前工程として必須であり、洗浄の良し悪しが殺菌効率に大きく影響する。十分な殺菌効果を得るためには、設備表面の洗浄をしっかり仕上げておく必要がある。
床、壁、天井等と充填・密封機等の開放系の設備、機器の洗浄はブラッシングや高圧洗浄および殺菌を兼ねた泡洗浄などが一般的である。
タンク、配管類、熱交換器(殺菌や冷却用)、充填機などの密封系の内面の洗浄には、通常、CIPが利用される。CIPに使われるアルカリ洗剤は、タンパク質や油脂等の付着有機物に対して優れた洗浄力を発揮する。アルカリ洗剤の主成分はカセイソーダであるが、水に含まれるカルシウム、マグネシウムと不溶性のスラッジを生成して、機物表面に付着することがある。これを防ぐため、一般にキレート洗剤や界面活性剤が添加されている。
酸洗浄は、製造中に生成する不溶性スケールや、アルカリ洗浄で生成した不溶性の皮膜等、無機質系汚れを除去するために使用される。酸洗浄の主成分は硝酸の場合が多く、界面活性剤を添加して浸透性、すすぎ性が強化されている。
いずれも使用する洗浄剤の種類、成分、使用基準をよく確認した上で、汚れの種類や状態によって正しい洗浄剤の選定を行う必要がある。CIP等で洗浄液や熱水等が繰り返し使用される洗浄方式の場合には、使用液が過度に汚れることのないように日常の点検が重要になる。
②殺菌
製造ラインの殺菌には、熱や紫外線灯の物理的殺菌法と次亜塩素酸ナトリウムやエタノール、過酢酸水素等の薬品を用いた化学的殺菌法がある。殺菌効果の確実性、安全性、排水処理への負荷から考えると、加熱殺菌法が好ましい。しかしながら設備によっては加熱するのが困難な場合もあり、このような設備・装置については薬剤殺菌を適用する。
加熱殺菌法は熱水やスチームを用いて、飲料水が接触する器具や設備、熱交換器(プレート式や多管式など)、タンク、配管類の内壁等の殺菌が行われる。
殺菌剤として広く使用されている薬剤は、塩素系化合物およびヨウ素系化合物からなるハロゲン系と、第4級アンモニウム塩と酸、アニオン界面活性剤からなる界面活性剤系、および過酸化水素や過酢酸といった過酸化物系の3つに大別される。
薬剤殺菌で最も注意しなければならないことは、製品飲料水への混入(コンタミ)防止である。そのため飲料水が直接接触する機械、器具、容器などに使用する場合は、十分なすすぎを行い、薬剤の残留がないようにしなければならない。薬剤残留リスクを逃れるために、食品添加物でもある次亜塩素酸ナトリウムやエタノール、電解水など安全面から広く用いられている。
採用する殺菌剤については、耐性菌等を考慮し、適用対象と殺菌効力、および薬剤の化学的性質を十分に認識した上で、設備・装置や製造工程ごとに要求される微生物清浄度に応じて使用し、過剰な薬剤の使用は避けるべきである。使用される薬剤は、従来、対象とする微生物への有効性に重点が置かれていたが、消費者および工場作業者への安全性と排水処理負荷の少ないものへとシフトしてきている。使用環境や使用対象物に適合し、有効性で適確な効果を発揮すると同時に、製品や人にもそして環境にもやさしく安全で安心できる薬剤を選定する必要がある。
3.環境管理
飲料水製造工場での微生物の増殖を抑えるためには、洗いやすく、液溜りのできないサニタリ構造の床面、機械設備・装置、配管等が必要になる。また、微生物の増殖には水分が必須であることから、工場内の床や壁はできるだけ乾燥状態に維持することがポイントとなる。
飲料水を代表とするミネラルウォータは、無味、無臭、無色に近い特性から、飲料水の接液部だけでなく、工場環境中の匂い、呈味成分や浮遊微粒子、浮遊菌などの影響を受けやすいため、徹底した環境管理が必要となる。特に、飲料水および充填容器を別々に殺菌して無菌環境下で充填・密封を行う場合は、二次汚染防止のため、充填容器の殺菌から充填・密封工程までの清浄度の高いクリーンゾーンにする必要がある。このためHEPA等の高性能エアフィルターを通した無菌エアを充填室内や装置内に供給することで、浮遊塵埃量を一定の基準以下に抑えたクリーンルームや局所的なクリーンブースを利用することが一般的になっている。
①クリーンルーム
クリーンルームはその清浄度によってクラス分けがされている。通常、充填・密封ゾーンを最も高い清浄度(クラス100程度)にして、周囲よりも陽圧(10Pa程度)を保ち、隣接するエリアを順次低い清浄度(クラス1,000~10,000)に下げていく方法が採用されている。
クリーンルームの清浄度を維持管理するために、次の4つの原則がポイントとされている。
- イ) 塵埃を持ち込まない
- ロ) 塵埃を発生させない
- ハ) 塵埃を速やかに除去する
- ニ) 塵埃を堆積させない
イ)、ロ)の塵埃を持ち込まず、発生させないために、製造工程作業者は手洗い後、全身を覆う無塵衣やマスクを装着し、粘着マットやエアシャワーを通って清浄ゾーンへ入室する。また、物品の搬入もパスボックスを介して行うが、段ボールや鉛筆などの発塵媒体の持ち込みは禁止するといったこまめな配慮が必要となる。ハ)、ニ)の発塵を除去し、堆積させないためには、室内の空気の流れの方向と速さを極力均一にして、陽圧を保ち、静電気の発生を抑えるとともに、床の隅、角の部分に丸みを付け、水平面の少ない傾斜を付けた構造にした上で、定期的な拭き取り清掃を実施することが衛生管理上重要となる。
クリーンルーム内の清掃作業は、清浄方法と頻度から、その日に堆積した塵埃を除去する「日常清掃」と、日常では対応できない箇所の「定期清掃」、および間仕切り変更時や装置搬入時および清浄度管理レベルの値が超えた場合や事故対応時等に行う「特別清掃」の3つに分類される。クリーンルームの清浄度を安定維持するためには、それぞれに対応した清掃計画を立案し、その計画を基に清掃を確実に実施することが重要である。
なお、クリーンルーム内全域の環境殺菌を効果的に行う方法として、以前はホルムアルデヒドの燻蒸が行われていたが、近年は規制が厳しくなったため、過酸化水素ガスを使った環境殺菌の導入が主流になっている。
②環境モニタリング
クリーンルーム等のクリーンゾーンの製造環境の清浄度の維持、管理を確実に実施するためには、清浄度の異なるゾーンごとに、浮遊微粒子、空中微生物および表面付着微生物のモニタリングを行う必要がある。モニタリングの個所、頻度、対象微生物を決め、具体的なモニタリング方法を定めるとともに、その評価基準(判定、処置、警報等の基準)を設定して、維持、管理することが重要となる。一般的に、浮遊微粒子はパーティクルカウンターで計測し、空中微生物は浮遊菌や落下菌を培地に捕集してその数を調べる。また表面付着菌は拭き取り法やスタンプ法で検査する。これら検査の頻度は、最も清浄度の高い充填・密封ゾーンでは製造日ごとに、他の清浄ゾーンでは週に一回程度、非清浄ゾーンでは1~2ヶ月に一回程度の検査が実施されている。
③汚染防止バリア
充填・密封工程を最上位清浄ゾーンとする無菌環境を維持するためには、クリーンルームのほかに、無菌と非無菌との境界にバリアを設け、微生物の混入・汚染を防ぐ必要がある。このバリアには、主に、スチームバリアと差圧バリアおよび薬剤を用いたケミカルバリアがある。
スチームバリアはタンク接続部や撹拌機、ポンプ、ホモゲナイザーの摺動部等に利用され、スチームの温度(圧力)と保持時間が管理ポイントとなる。
差圧バリアは、クリーンルームとアイソレータ等、清浄度の異なるゾーンの境界や、清浄区域と汚染区域の境界、およびアセプティックタンクと周辺雰囲気との境界などに差圧を設けて、微生物汚染を防ぐ方法である。それぞれの差圧の指標は国によって異なり、あるいは隔てられた清浄度の差により異なってくるが、おおむね5~15Paである。
ケミカルバリアは主に充填容器および製品の搬送コンベアやリテーナーが無菌ゾーンに入ってくる箇所に使われ、薬剤濃度、温度、接触時間が管理ポイントとなる。交換部品や検査備品をクリーンルームに持ち込む時の薬剤による噴霧や拭き取り殺菌もケミカルバリアの一つといえる。
以上
【参考文献】
- 高野光男ほか:食品の殺菌-その科学と技術-(1998)幸書房
- 横山理雄ほか:食品の無菌包装-その技術とシステム化-(2003)幸書房
- 松田晃一:おもしろサイエンス飲料容器の科学(2018)日刊工業新聞社
- 大鶴 勝ほか:食品加工・安全・衛生(2007)朝倉書店
- (社)日本空気清浄協会:クリーンルームにおける清浄化指針No.27(1992)