2023/06/05
『食品製造プロセスの自動化アプローチ』
An automated approach to the food manufacturing process
はじめに
製造システム構築にあたっては、少し時代を先取りする意味からも、現状に妥協せず攻めの姿勢、かつ新規性を重視することが大切である。そのためには現状の問題を共通化し、組織を越えたチャレンジが必要になってくる。つまり組織間のコンセンサスを深め、理想的にはシステムと人が一体となって活動できる製造システムを構築することが自動化として求められる。
1.自動化アプローチのターケット
食品製造プロセスで、自動化アプローチとなるのは、プロセスにおいてボトルネックとなっている項目となる。表1. にボトルネックとなっている項目の概要を示す。
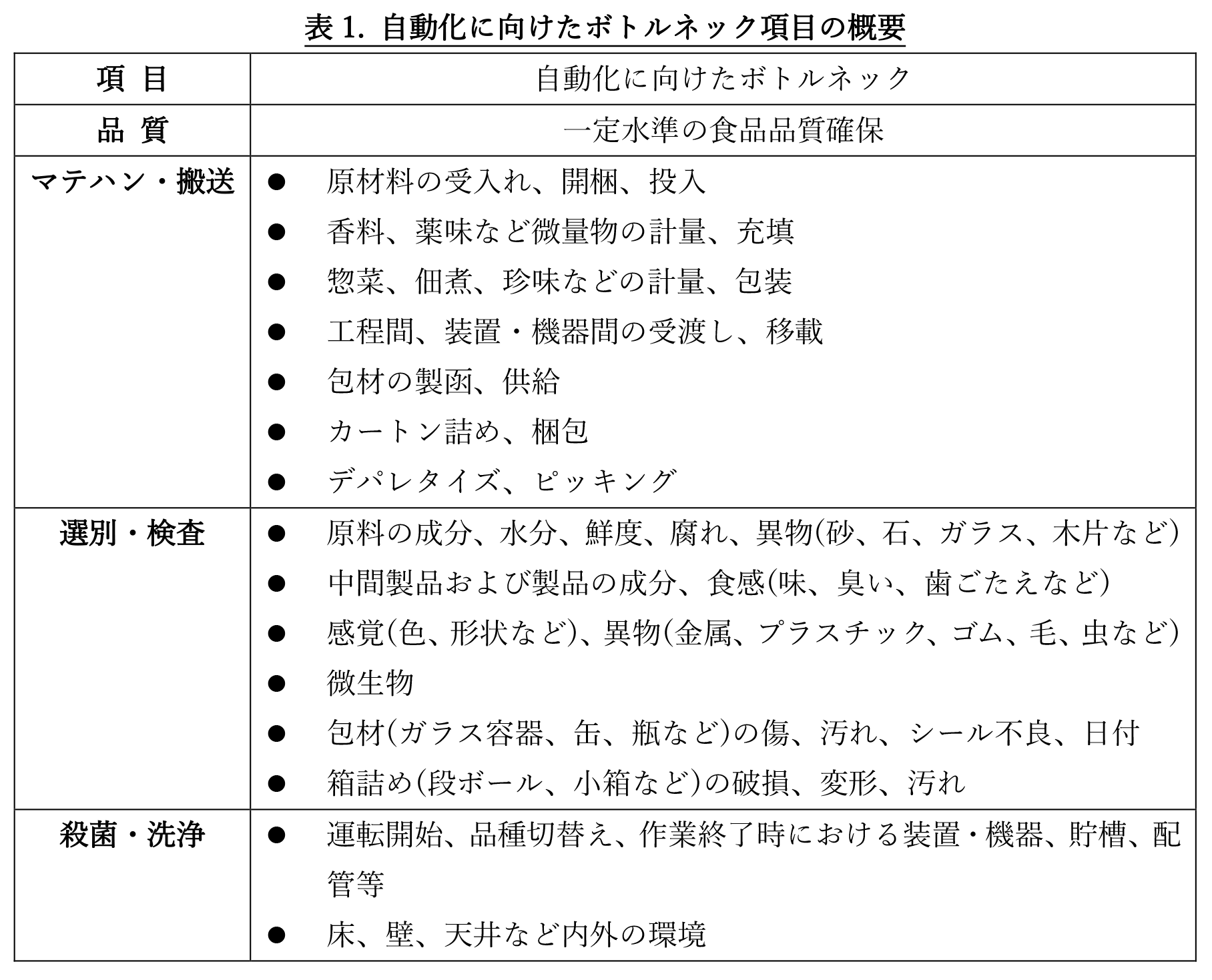
表1に示したように、第1に一定水準の品質確保、第2に全工程に関わるマテハン・搬送、第3に原料・製品・包材の選別・検査、第4に品種切替え、運転終了時の殺菌・洗浄などがあげられる。この中でいくつかは解決されているが、食品工場のほとんどの多くは、これらボトルネックに対する開発を要するものである。
食品を一定水準の品質に、コントロールするのが困難とされている要因の主なものは、次の3つといえる。
(1) 原料が天然物のため、それに含まれる成分は、微量な物まで入れると無限に近く、物理的、化学的に見ても、成分組成、組織、構造が極めて複雑な系の物質で、しかも品種、産地、天候などによって変動する。
(2) 食品は温度、光線、空気(酸素)、衝撃・振動・圧縮および微生物の影響を受けやすく、きわめて不安定な物質である。
(3) 計測対象が、取り扱いの厄介な粉体、固形物、柔軟体などが多い。
このように食品は、不安定な物質から成り立っているため、化学的、物理的メカニズムが不明なことが多く、計測の対象とすべき情報が定まりにくい。しかも制御のモデル化、つまり厳密な意味での加工条件の標準化が難しく、一定水準の品質を確保するのに「勘と経験」が頼りという現状がある。しかし、勘と経験に頼っていると進歩がないし、自動化は到底不可能になる。また食品製造業全体の深刻な熟練者不足、人手不足も解消しない。近年、これらの課題解決に向けた新技術としてAI技術への関心が高まっている。
この厄介な食品に適したセンサが見当たらないという現場サイドの言葉を聞くことが多い。確かに品質の決め手になる成分を直接、かつ迅速に計測するセンサが少ないことは事実である。このような状況の中で自動化を進めるのは困難を極めることになっているが、自動化の道を開くための着眼点は、品質に関わる定性的、かつ定量的な加工データを数多く収集して、これらのデータを基本に、品質と密接な関係にある要素を探し、AI技術などを活用してモデル化を試みながら最適解を見つけることである。その際、できる限り既存の各種センサ技術で計測が容易で、精度、再現性の高い物理量に置き換えることが大切である。例えば、温度、圧力、pHといった物理量およびその変化(パターン)がどのように品質に関わっているのか追跡するのも一つの方法である。このような方法によって、自動化を実現した事例としてあげると、大豆蒸煮の均一化、製麺装置の無人化、結晶缶の無人化など挙げると事例には事欠かないほどの成功例がある。
製造プロセスを自動化と言う観点から捉えると、運転操作を中心とした「運転」、運転状況を把握するための「監視」、あらかじめ設定した品質・量が確保されスケジュール通りに進捗しているか、収率は、稼働率は、などを確認する「管理」の三つに分類できる。表2. にそれぞれの現状分析、改善の検討項目を示す。
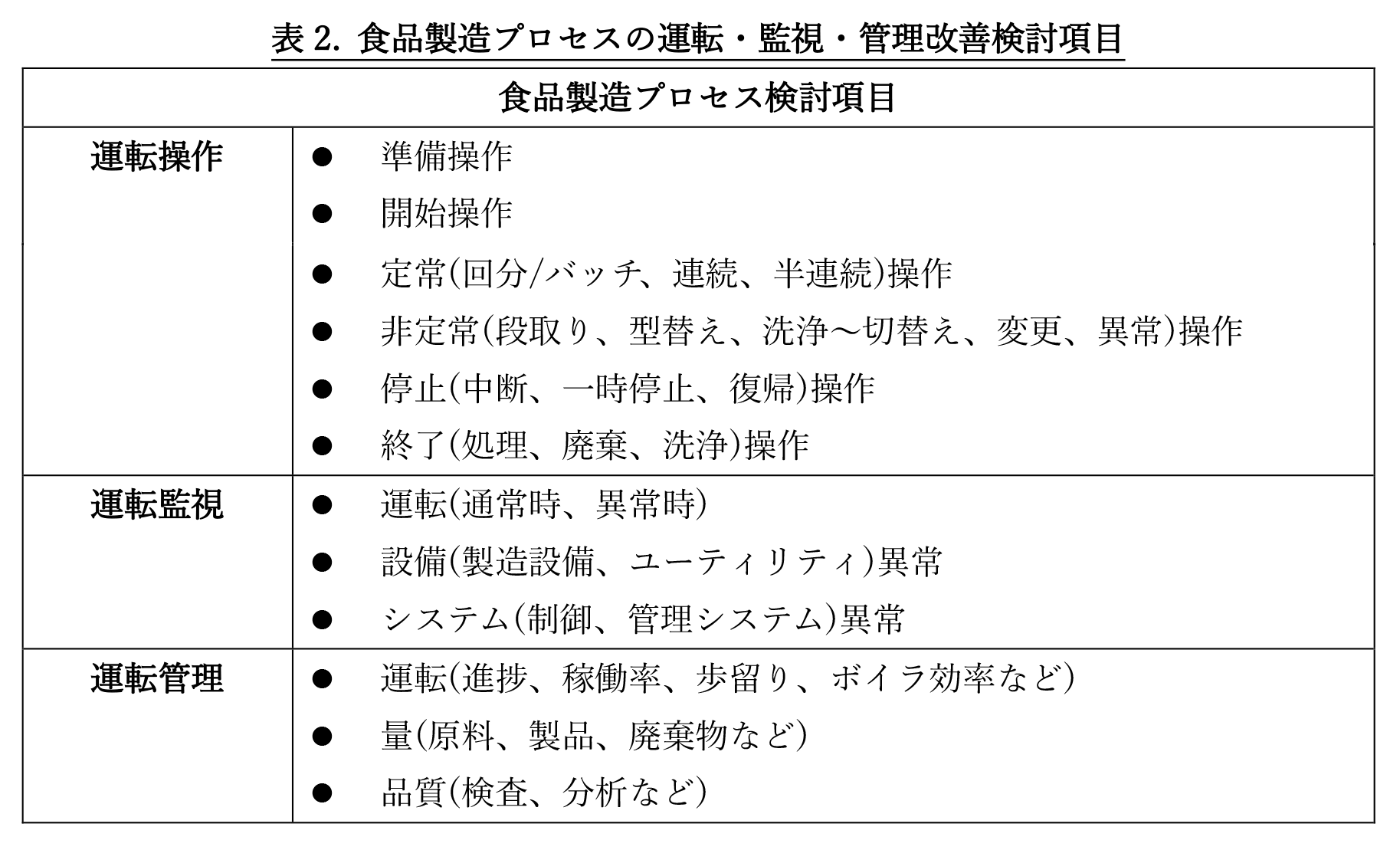
運転を準備から終了まで、6つの操作に分類し、その要点について詳述する。
(1) 準備操作は、原料の受入れ、開梱、投入、加工装置・機器類の洗浄、ジグの取付け、ユーティリティ(ボイラ、コンプレッサ、排水処理など)の段取りや、確認が必要になる。これらを自動化することはきわめて難しく、人に依存するところが多い。従って、むしろ確認を含めて作業能率を高めるための工夫、つまり作業改善を主眼に置くことである。特に原料関係では荷姿が紙袋、斗缶、瓶など多種多様なのが現状で、搬送、マテハンに多くの人手を要している。荷姿の変更、開梱機の工夫を含め検討することが重要である。例えば、紙袋をコンテナバックにして大幅な人員削減を実現した例もある。
(2) 運転開始操作は自動化の導入が比較的進んでいて、その効果は非常に大きい。例えば、複数個のバルブ、ポンプ、撹拌機などを一度に操作することは不可能であり、操作順序が決められていたりすると、人手では間違いを起こしたりするリスクが高い。従って、このような場合は自動化の威力が十分発揮できる。つまり自動化の制御方式でいえば、シーケンス制御の得意とするところである。
(3) 一般的に、素材型ラインの定常運転は、比較的人手がかからないが、混合・包装型ラインでは、人手を要する場合が多い。これは、加工工程は勘と経験に頼ることが多いこと、包装工程はライン前後、装置・機器間の継ぎなどに人手を要している。このようなところに着目して、自動化に取り組むことである。
(4) 非定常操作は、自動化のポイントになるところで、運転条件変更、品種切替え操作、異常処理操作などが考えられる。これらの操作は稼働率に大きく影響を与えるため、いかに早く、確実にできるかが勝負である。
特に加工工程の品種切替え操作は、コンタミの問題や食品独特の洗浄・殺菌の問題が大きく関わってくる。また包装工程では、型替えなど問題になる。
ここで取り上げた非定常操作の3項目につき、掘り下げ分析、改善を実施し、自動化を指向することである。
ここで、食品プロセスの洗浄について詳述する。密閉型の食品機械、タンク、配管などの洗浄に、古くから定置洗浄といわれるCIP(Cleaning In Place)方式が採用され、自動化を組み込んだ洗浄システムとして液体系のプロセスで多くの導入されている。しかし、多勢を占める食品機械や、厄介な粉体、固形物、柔軟体を扱うプロセスでは、相変わらず洗浄が最大の悩みになっている。
開放型の食品加工機械の洗浄システムとして、6自由度を持った多関節走行型ショルダロボットを壁面に沿って走行させて、複数の開放型の食品機械を順次フォーミング洗浄する自動洗浄するもので、食品製造設備としての洗浄ロボット技術、特に耐環境条件および衛生・安全条件を克服し、導入された事例もあるが、開発でのハードルは高いものがある。細菌テストにおいても、人手による洗浄に比べはるかに良い結果を得ている。また稼働率向上に有効なデータもある。技術革新がここ数年で進展し、機械要素部品も食品プロセスのような高湿で塩分を使用する環境に適していて食品衛生法に適合したものが上市されている。
洗浄の基本は、装置・機器のサニタリ化を図り、装置・機器の分解、洗浄時間の短縮など、洗浄効率を上げるための工夫と、CIP洗浄が可能になるように設備上で工夫することが重要となる。
(5) 停止操作とは、運転の都合や故障などによって一時停止することを指し、この時間は数分から数十分で食品品質に致命的な打撃を与えないで、再復帰が可能な範囲になる。この操作は、停止・復帰手順、停止時間中の品質維持条件に基づいて行われる。従って、品質に関わる諸条件を分析し、これらの対処手順、条件を決めることがポイントになる。
(6) 運転終了操作は、すべての運転を停止し、作業を終了することを言う。素材型ラインのような連続プロセスでは、年間に多くて数回の運転終了操作であるが、混合・包装型ラインでは毎日運転終了操作がある。運転終了操作は、必ず運転開始操作が順調に行われることを前提に検討することになる。
ここまでに詳述した6つが運転に関わる操作の主なものである。これら自動化からみた基本運転操作を参考にして、分析・改善を進め、結果としては、このように細分化した運転操作に区分して、自動化の基本構想を確立することである。
2.食品プロセス自動化の基本事項
フレキシブルな食品プロセスシステムを構築する場合、食品プロセスは、「バッチ(回分)」、「連続」、「半連続」のどの方式が適切なのか十分考慮しなければならない基本事項となる。これは食品プロセスの内容によって異なってくるが慎重さが要求される事項になる。食品プロセスは、バッチ方式が主流と言える。連続プロセスの場合、どうしても条件が限定されるため、新しい品種、品目の製造が不可能になったり、品種切替えの頻度が多くなるなど、洗浄などのロス時間が発生するなど不都合が発生してしまう点がネックとなる。それに対してバッチプロセスの場合、フレキシビリティを持っているため、いざというときには人海戦術で運転操業が可能とすることができる。いずれの方式を選択するか、あらゆる視点から現状を分析し、最善の方式を導入することが大切である。
3.食品製造プロセスの運転監視の要点
運転監視とは、生産指示通りに、正常運転を行うために、ユーティリティを含む製造設備、およびそれを制御、管理するシステムが正常に機能しているか、言い換えるとトラブルが発生していないか、確認することをいう。
食品品質に関わらないレベルでないトラブルが発生した場合、不良品をつくらないためにラインを止めることになり、食品ロスとなる。食品プロセスにおいては、ラインをとめることを前提に運転監視をするわけにはいかないので、トラブルを未然に発見、防止することがより重要となる。すなわち「予知・予告」を重点に分析、改善を行うことになる。例えば、異常温度になればトラブルで、異常温度になりそうだ、なるだろうといった予知ができるかである。達温時間を常時監視し予知する、撹拌機の負荷変化と温度に相関関係があれば、そのデータから予知する、など予知方法が考えられる。近年、IoT技術やAI技術を駆使して予知する予知保全技術も提案されている。これらの技術を活用したエキスパートシステムに製造現場オペレータの経験、スタッフの技術などを集約し、生産技術に関わるノウハウをシステム化できれば自動化技術の助けになるといえる。
自動化という面から、オペレータは何を監視するのか、あるいは何をオペレータに知らせればいいのか、予知・予告を前提に検討をすることがポイントになる。
4.食品製造プロセスの運転管理の要点
運転管理の要点は、まず生産指示通り食品品質は常時管理限界値になっているか、生産量は落ちていないか、などの基本的な管理を充実させることがポイントである。
食品工場は一般的に原料使用量、中間製品出来高、廃棄物処理量といった「量」の管理の不備が以前は多く問題となっていた。特に近年では、食品ロスの問題につながることから改善が必要になってきていた。以前までの「どんぶり勘定」のようなことをしていると、十分な歩留りや原価管理ができないし、改善点も見つけることができない。まずは第一重点管理項目に、少なくとも品目毎の歩留り、原価が明確になるように、改善を進めることである。また生産が小ロット、多品種化してくると、販売との関係で、製造品の仕掛がどうなっているかも重要になってくる。
製造としては、品目毎の進捗状況を常時把握する必要があり、それに対し生産変更が発生した場合は、適切な指示を与えられる仕組みを確立することが大切である。すなわち第二の重点管理項目は、進捗管理の確立である。
5.最後に
「食品製造プロセスの自動化アプローチ」を考える場合、食品製造プロセスの運転操作、監視、管理の改善を進め、製造プロセス全体の最適化を図った構想立案に結び付けることが重要である。
以上
【参考文献・引用先】
- 「食品工業のファクトリー・オートメーション」草間和彦 著 光琳
- 「食品工場の生産技術」弘中泰雅 著 日刊工業新聞社
- 「食品製造業の自動化の現状と抱えている課題」技術レポート2023/05/08
木本技術士事務所HP https://www.kimoto-proeng.com/report/3408 - 「食品工場における自動化 (FA化) に向けた考え方」技術レポート2023/05/22
木本技術士事務所HP https://www.kimoto-proeng.com/report/3440