2023/08/04
『FA化推進チームの活動コンサル事例』
Activity consulting case of the FA promotion team
1.はじめに
FA化を進めるにあたって、ユーザーの立場になり取り組み、支援・アドバイスを行った時のFA化推進チームの役割と要点を実際の経験に基づいて、順を追って紹介することにする。
食品会社を訪問すると、まず次のような何とかしたいといった抽象的な言葉をよく耳にする。
(1) 専門スタッフがいないし、技術力がない
(2) 何から手を付けていいか糸口が見つからない
現在、立派な製品をいくつも送り出している多くの企業の人々から聞く言葉ではなく、おそらく厳しい企業環境下で、かつてない過去に経験しなかった技術革新や人手不足への対応、生産性の効率化の要求などのため、何とかしようという“企業の焦り”の現れと感じる。
2.FA化を推進するために必要なことは何か
FA化を推進するためには、企業として今まで積み上げてきた生産技術のほかに、ハイテクノロジ、食品関連以外の幅広い技術を加えた「総合技術力」をいかに発揮できるかが、鍵になるといっていい。つまりFAは『新しい生産システムを狙いとした抜本的な改善』であり、『価値の創造』といえる。
そこには企画力、技術力、判断力に加えて、ノウハウ、組合せ、統合といった技術力、さらに人間の知的な活動を活性化するための動機、好奇心、やる気などが最も重要になってくる。また今までのような延長線上でものを考えるのではなく、固定概念から脱皮し、視野を広げ、視点を変えることによって、生産技術を探求することが求められる。すなわち、『発想の転換』が要求されることになる。
このようなことからFA化を進める場合、「協力体制」が取れるか、また外部の力を借りるとすれば、よきアドバイザーを選択できるか、指導力を発揮できる人がいるか、などを検討することが重要になる。
図1. にFA化の進め方のフローを示す。
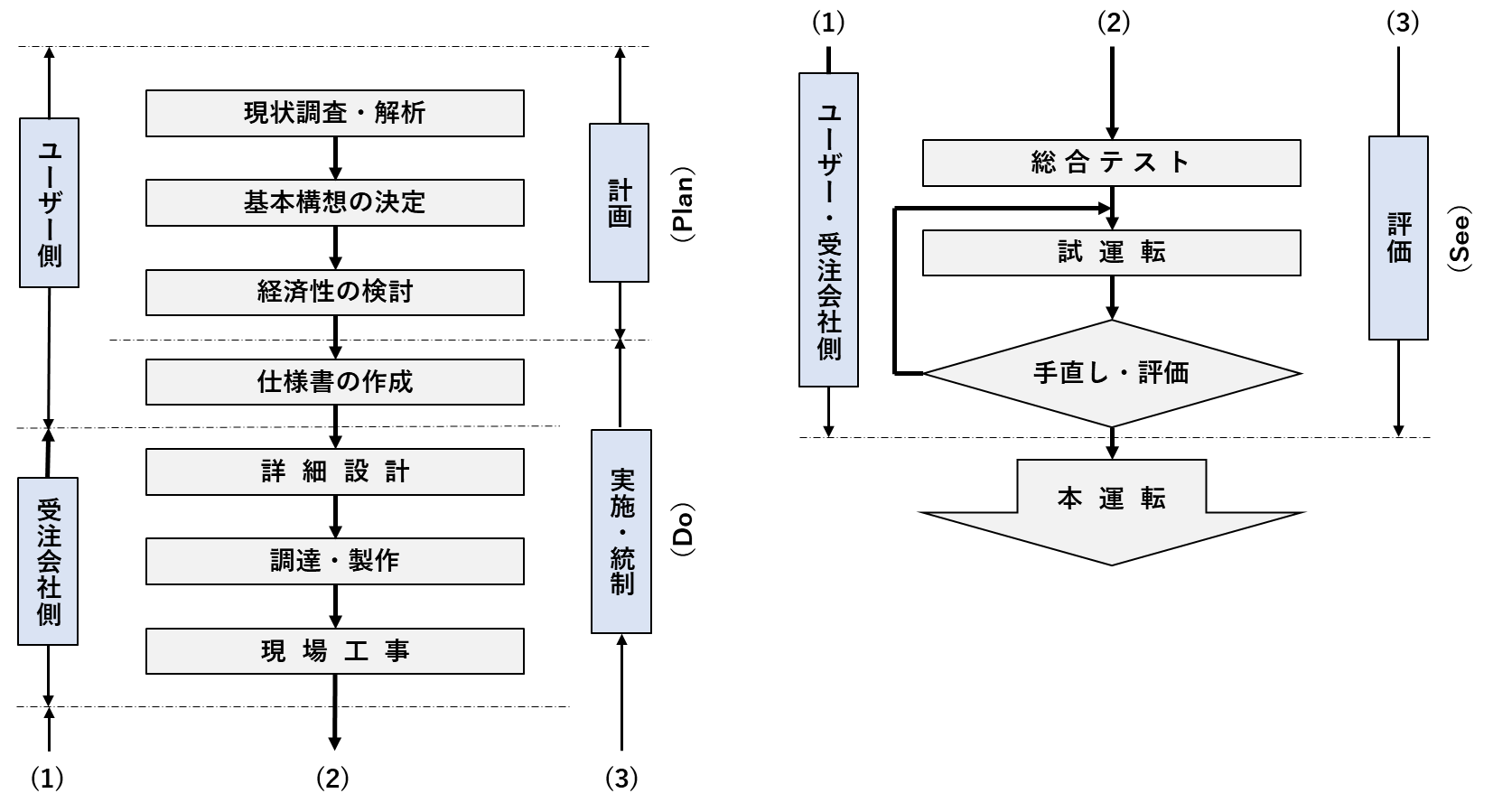
FA化を進めるために最初に提案するのが、プロジェクトチームとして5~6名から構成される「FA化推進チーム」の発足である。FA化を進める場合、自部署単独では進められない場合が多いことから、部門をまたがった横断的な人員構成とすることを提案し、はっきりとした目的、目標を掲げて、結果重視の組織的な「プロジェクト活動」とすることが必要である。
食品工場では専門スタッフがいない、設備部門がないなどの事情を抱えている場合が多い。このような事情は発足したプロジェクトチームが補い、少なくともユーザーとしては、計画段階から仕様書の作成まで、担当できるようにするのが望ましい。しかしながら自社だけで難しい場合は、スタッフの育成も兼ねて食品工場に精通しているアドバイザーがその役目を担うことで可能とすることができる。
FA化推進チームであるプロジェクトの扱う対象は、大は工場、小は工程を1つの単位として、図2.
に示すような5つのフェーズに分けてプロジェクトを推進する。
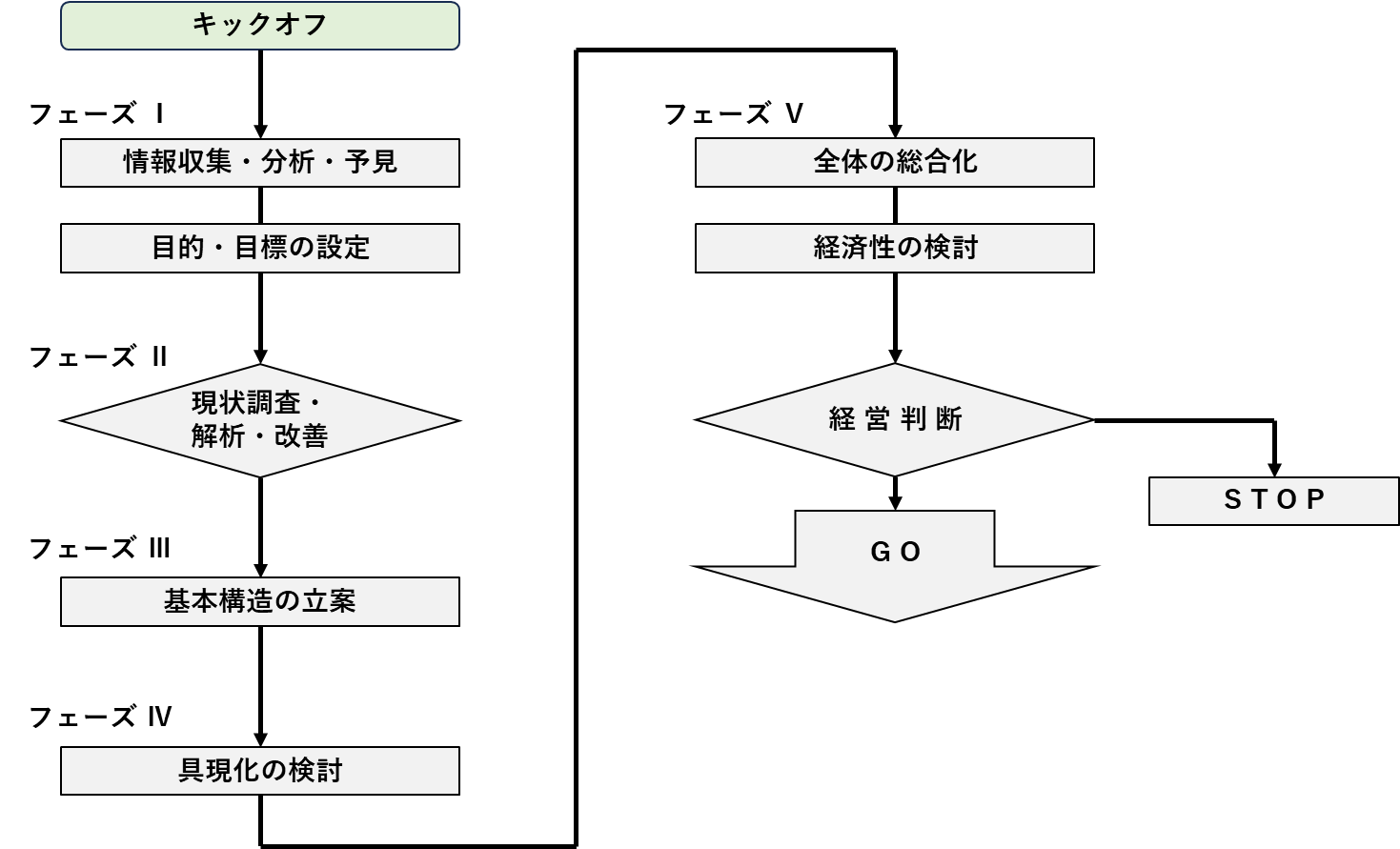
最終的なゴールはフェーズⅤでまとめられた答申書の提出をもってプロジェクトを完了し、経営の判断を仰ぐ資料となるものとする。紹介するフェーズⅠ~Ⅵまでの活動は6ヶ月を目安に計画し、推進した事例である。
3.活動フェーズⅠ:情報の収集・分析・予見および目的・目標の設定
このフェーズではプロジェクトを進める上で、メンバーが共有化しなければならない基本的事項を整理、確認し、FA化の目的、目標を設定する。つまりメンバーが現状を把握し共通認識することにより、共通のイメージを描き、FA化のステージを決める。FA化を進める上で最も重要なのは、はっきりとした“あるべき姿”をゴール目標に活動ストーリーを描くことである。
(1) 事業予見、前提条件の確認と明確化
そのためには、あらゆる視点から情報を収集し、分析することが必要で、まず1つ目にはそれを基に5~10年先の「事業予見」を試みることから始める。例えば、経営指標が過去数年間どのように推移してきたか、すなわち損益計算書に記載されている売上高、売上原価、売上利益、経常利益等々といったものから、賃金、原価償却費などの「固定費」、原料費、エネルギー費などの「変動費」がどうなっているか、限界利益(付加価値)、損益分岐点はどこあるのか、また労働分配率といったものまで細部にわたって解析する必要がある。
これらのデータは競合他社と比較して、どんなレベルにあるのか比較することも大切である。さらに過去、どんな製品、品目がどのように推移してきたか、P
– Q(製品 –
量)分析することも重要である。それによって将来の製品の伸びが想定することも可能になるので、事業予見を組み立てる参考にするとよい。
次に2つ目はFA化のための「前提条件」を明確にする必要がある。その項目として次のようなものがあげられる。
①
FA化の対象工場または工程と、その対象範囲(ストレージ、加工、包装、検査、保管、物流等々どの範囲までを含めるか)
② 1人当たりの年間労務費(男女別 / 従業員およびパート)
③ 年齢別人員構成(男女別 / 従業員 / 直接、間接両部門およびパート)
④ 組織と各セレクションにおける機能と役割
⑤ 操業条件と勤務形態(8、24時間操業、休日操業 /
交代勤務、残業、休日勤務形態、パート増大か、減少か、下請け比率は)
⑥ 投資採算性の基準(新設、更新、改善 / 省力化、省エネ / 回収年数)
⑦ 将来計画への対応(新事業、新製品、増産に伴うスペース確保、要員確保)
⑧
増産および自然増への対応(人件費、蒸気、電気、用水などユーティリティの増加
/ 排水の増加 / 品質検査、点検項目の増加)
⑨ プロセスのステージ(品種数、量、品質、収率、歩留りの状況 /
設備能力と制約条件、ラインの稼働率、品種切り替え頻度、洗浄時間 /
ハンドリング、搬送、流通の状況)
これら9つの項目につき4M「人:Man」、「物:Material」、「設備:Machine」、「金:Money」という観点から組織、運転などの運用を含め、現状はどうか、現在から将来に亘って制約されるものは何か、抜本的な改善どんなものがあるか、など前提条件として考えられることを洗い出しまとめることが重要である。
(2) 目的・目標の設定
事業予見、前提条件が明確になったところで、いったいFA化の目的(機能 /
使命、役割、任務)は何か、そして目標(目的の物差し、尺度 /
共通性のある状態、条件)をどのように設定するかということになる。
FA化の目標は、Q(Quality:品質)、C(Cost:原価)、D(Delivery:納期)の性能向上が第一次の重要な目標で、それにS(Safety:安全)、M(Morale:士気)、P(Productivity:操業度)向上を加え、より高度の総合生産性を構築することである。ここで注意すべきこととして、目標はなるべく理解しやすい言葉で表現し、できるだけ具体的に、かつ定量的な数値で表すことが最も重要になる。
目標の項目例は、次のようなものになる。
① 生産品種、品目とその生産量、能力の設定(新製品を含めるか)
② 商品ごとの品質基準(管理限界の設定)
③ コストの設定(コストダウンの%または金額で表示)
④ 最終要員の設定(長期か、年度ごとの要員計画 / パート、下請け)
⑤ 下請けの役割と範囲(中間製品、包装、配送などの下請化)
⑥ 可能投資額の設定
⑦
ジャスト・イン・タイムの設定(受注から出荷までのリードタイム、あるいは工程毎のリードタイムなどの設定)
これら7つの他に新事業のためのスペース確保、組織の機能と役割なども合わせて、目標設定に加えることが望ましい。いくつか洗い出された目標は重点目標に絞り込み、それに対して、個別の目標に落し込むことが大切である。よく掲げられる目標の例としては、「工程の安定化」、「省人化、省力化」、「品質の向上」、「省エネルギー」、「無人化」、「生産性向上(2倍とか、3倍とか)」などを多く見かける。
目標を具体化するためには、計画、設計、施工、各段階の大まかな実行スケジュールが必要になってくる。この段階では、目標を達成するためのおおよその予算と必要になる人員数も想定しておくことが肝要である。
このフェーズの大きな目的は、情報を共有化することによって、メンバーの認識を高め「FA化に取り組む心構え」を確認し、新しい技術に挑戦する意欲をどのように持たせるかが鍵を握ることになる。
4.活動フェーズⅡ:現状調査・解析・改善
(1) 改善はFA化の第一歩
フェーズⅠで「事業予見」、「前提条件」が明確になり、次にこのフェーズⅡでは、実際の活動を開始することになる。まずあらかじめ決めたFA化の対象工場あるいは工程の的確な実態把握が必要になる。小は生産に関わる「原料、中間品、製品などの物性」、「設備の機能と能力」、「運転開始から終了に至るまでの単位操作」、「各種検査方法」、「トラブル時の対処」といったものから、大は原料や製品流通に関わる原料の産地、運搬方法、荷姿、種類、貯蔵方法、さらにこれらに関する運転管理、生産管理、販売管理といった情報処理など、十分に理解する必要がある。
FA化計画にあたっては、「物」、「設備」、「人」などのリソース(資源)および生産を支援する「情報」という観点から細部に亘って、会社レベル、工場レベル、プロセスレベル、それぞれにつき適用対象を十分把握することで、問題点を洗い出し、解決すべく改善を図り、標準化し、具体化へと進める。ここで最重要となるポイントは『改善はFA化の第一歩』ということである。
ここでフェーズⅡを進めるにあたって、心得として次の5つをあげておく。
① 現状をありのままに調査、改善にあたる
② 改善にあたってはいたずらに現状に妥協しない
③ 常に総合システムに心がける
④ アウトプットが意思決定につながること
⑤ 周到な行動計画を立てること
などである。
(2) 改善の出発点は技術標準書の作成から始める
フェーズⅡの具体的な進め方を図3.のフローに示す。図3. に示すように、現状把握、解析、改善を行うためには、どうしても現在使用されている生産に関する各種の技術資料が必要になってくる。
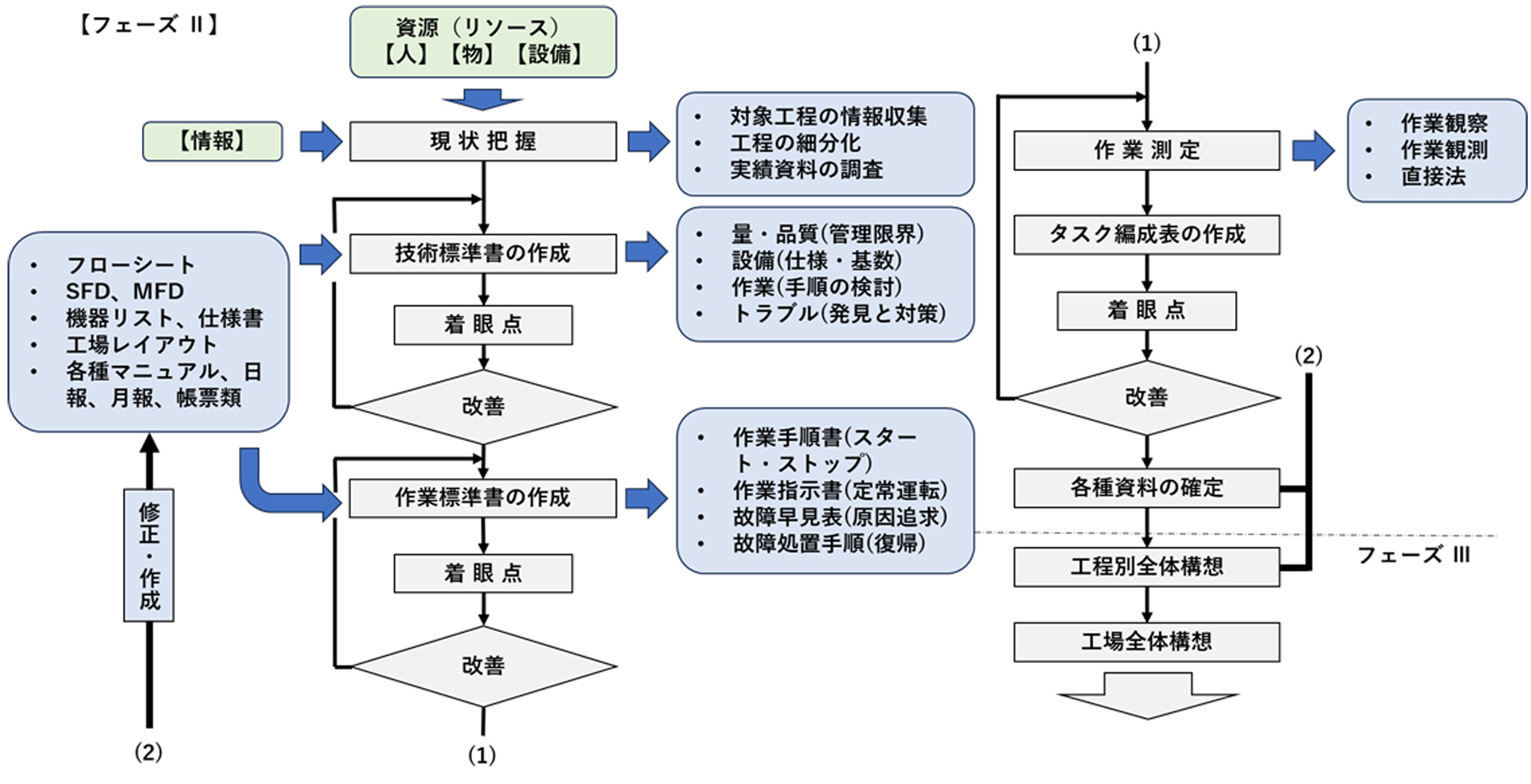
その主なものは、次のようなものになる。
①
マテリアルバランスシートまたはフローシートのいずれかで、原料から製品に至る過程で、原料、副原料、添加物、水、蒸気など物質バランス(物質収支の計算、ユーティリティの計算)が明確になる資料。
② 計画の最初に使われるSFD(Simplified Flow
Diagram)、詳細設計の段階で使用するMFD(Mechanical Flow
Diagram)、あるいはP&ID(Plant & Instrument
Diagram)、工程(分析)図記号のいずれか、物の流れが図面上で理解できる資料、図面上のシンボルは極力JIS記号を使用し、社内で標準化されることが望ましい。
③
機器(計器類を含む)に関するリスト、仕様書、図面、取扱説明書、ダクト図、配管図、配線図、計器盤、動力盤などの資料。
④ 工場レイアウト(全体配置図、建築図面、設備レイアウト /
機器配置図)に関する資料。
⑤
ユーティリティ(蒸気、電気、工業用水、市水、プロセス空気、計装空気)負荷バランス、排水処理施設負荷バランスなどの1ヵ月、あるいは1日の負荷変動に関する資料。
⑥
品質検査基準、運転スケジュール、運転操作マニュアル、運転日報、月報、各種実績資料などの管理資料。
⑦
運転管理、生産管理に関わる各種指示書、帳票類、帳簿、実績集計表、報告書等の資料、この他に組織と要員の役割を明記した資料。
ここに挙げた資料を揃えるのが難しい場合は、これらに類似した資料を数多く集めることである。一般に、食品工場の素材型ラインでは比較的このような資料が揃っているが、混合・包装型ラインでは、機械設備と直接対応することで間に合っているのか、個々の機器図面はあっても満足できる資料が揃わないのが実情である。
改善を進めるためにどうしても必要な資料については、この機会を活用して整備することが大切である。ここで最終的に残したい資料は、次のようなものになる。
① 物質バランスが理解できるフローシート
②
物の流れが理解できるP&ID(配管、バルブ、ポンプなどの個々のサイズ、計装表示まで記入した詳細図面)、また混合・包装型ラインは、理解しやすい工程(分析)図記号も準備する
③ 設備が理解できる機器図面およびマニュアル
④ 工場レイアウト(全体配置図、設備レイアウト / 機器配置図)
⑤ 品質検査基準
⑥ 運転マニュアル
⑦ 帳簿、帳票など標準化された資料
⑧ 技術標準書
などである。これらの資料は、名称、番号、シンボルなど、この活動を機会に工場内で統一した標準化を実施することも重要である。
「技術標準書」は、生産設備の解析・改善・検討資料として重要な資料になる。技術標準書は、現在手持ちの資料や、運転実績、個々の作業者が持っている技術情報などを基に「量・品質」、「設備」、「作業」、「トラブル」の4つの要素で構成するとよい。それぞれの書式例を表1.~表4. に示す。
表1, 技術標準書「量・品質」の書式例
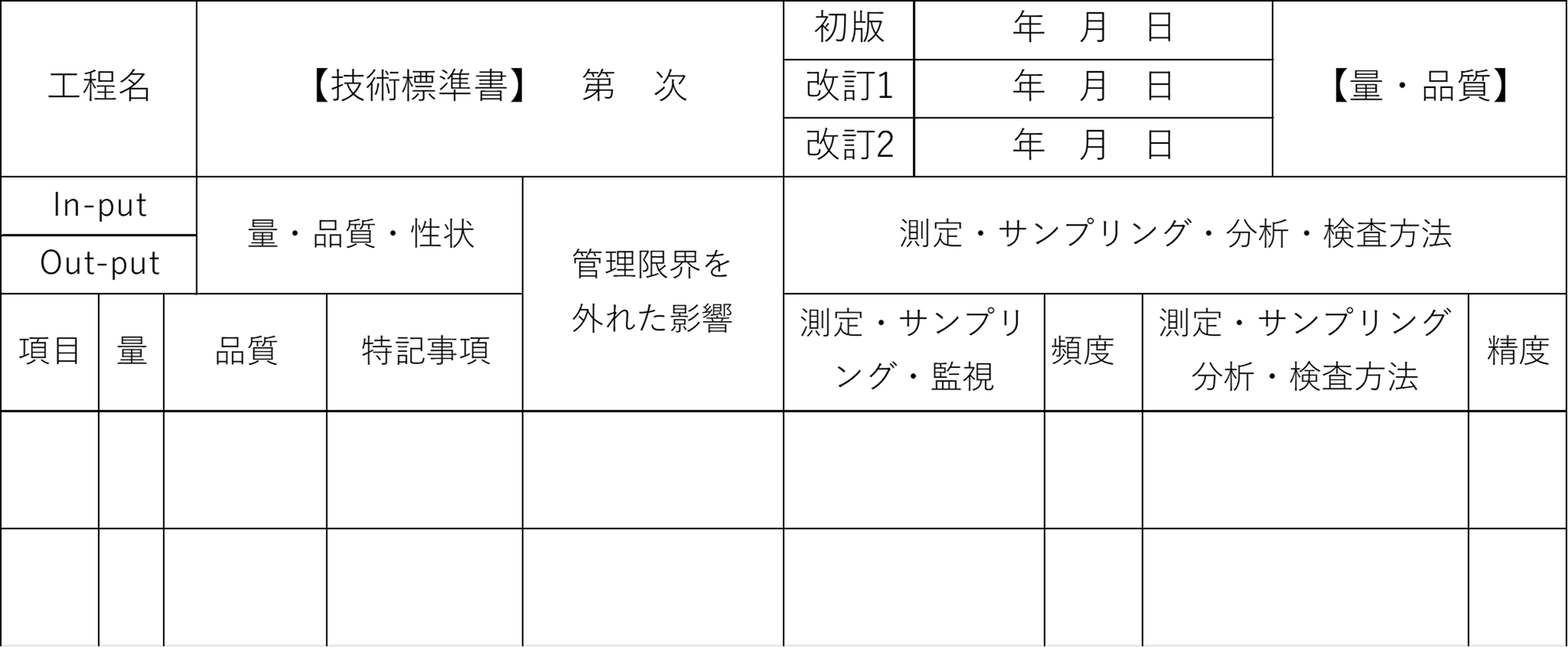
表2, 技術標準書「設備」の書式例
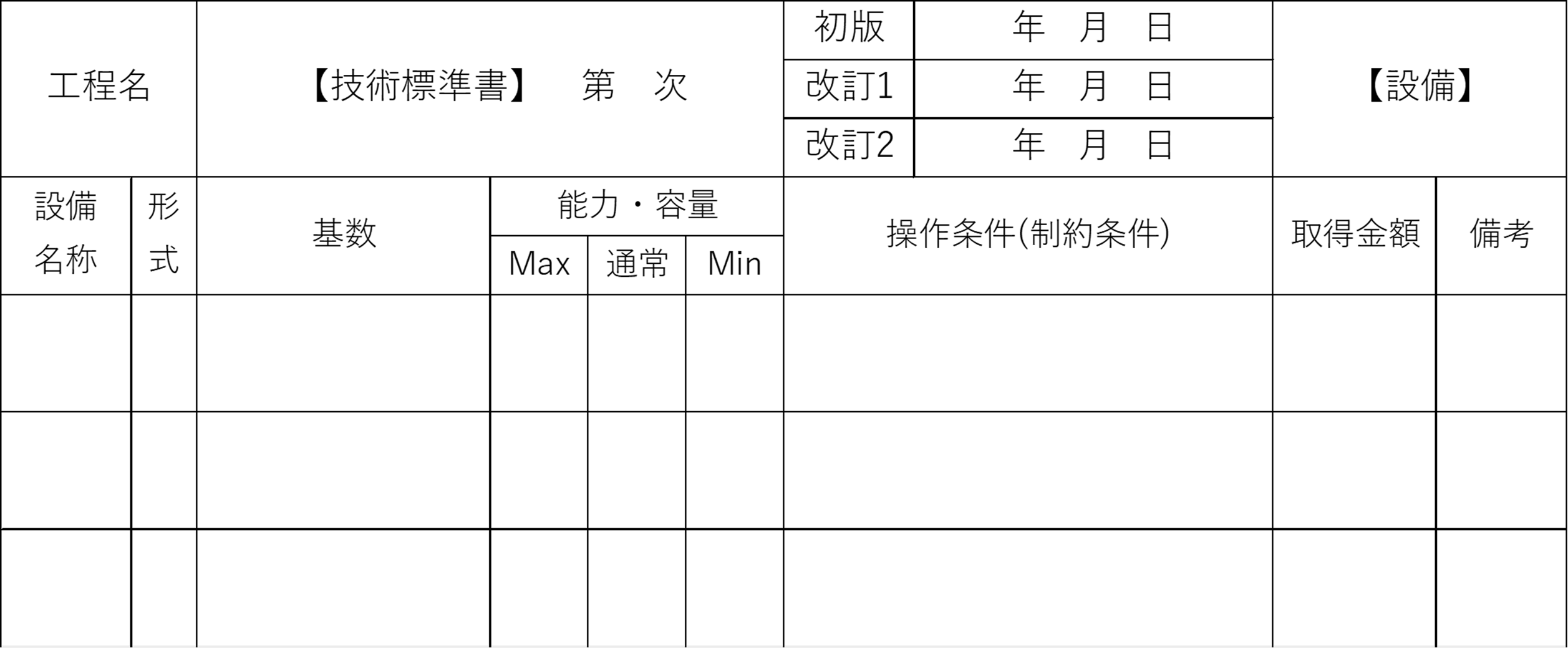
表3, 技術標準書「作業」の書式例
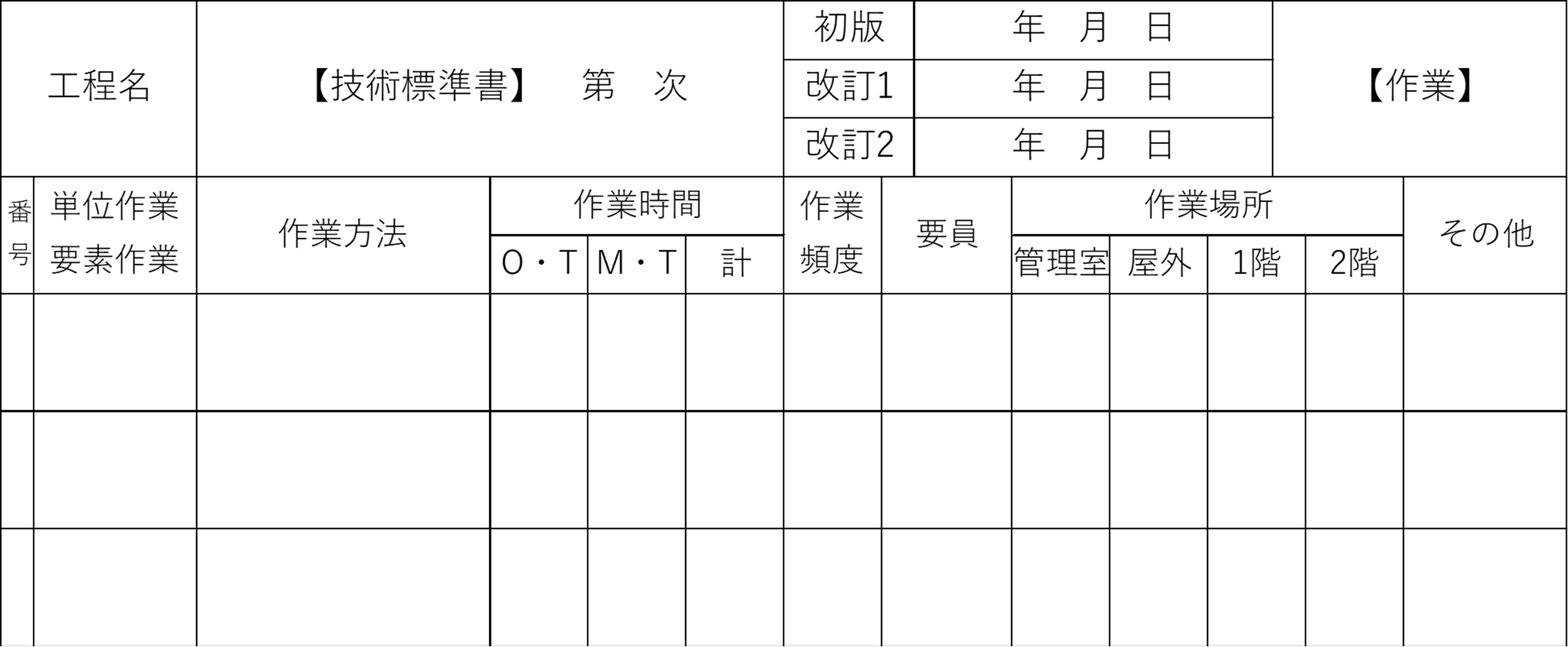
表4, 技術標準書「トラブル」の書式例
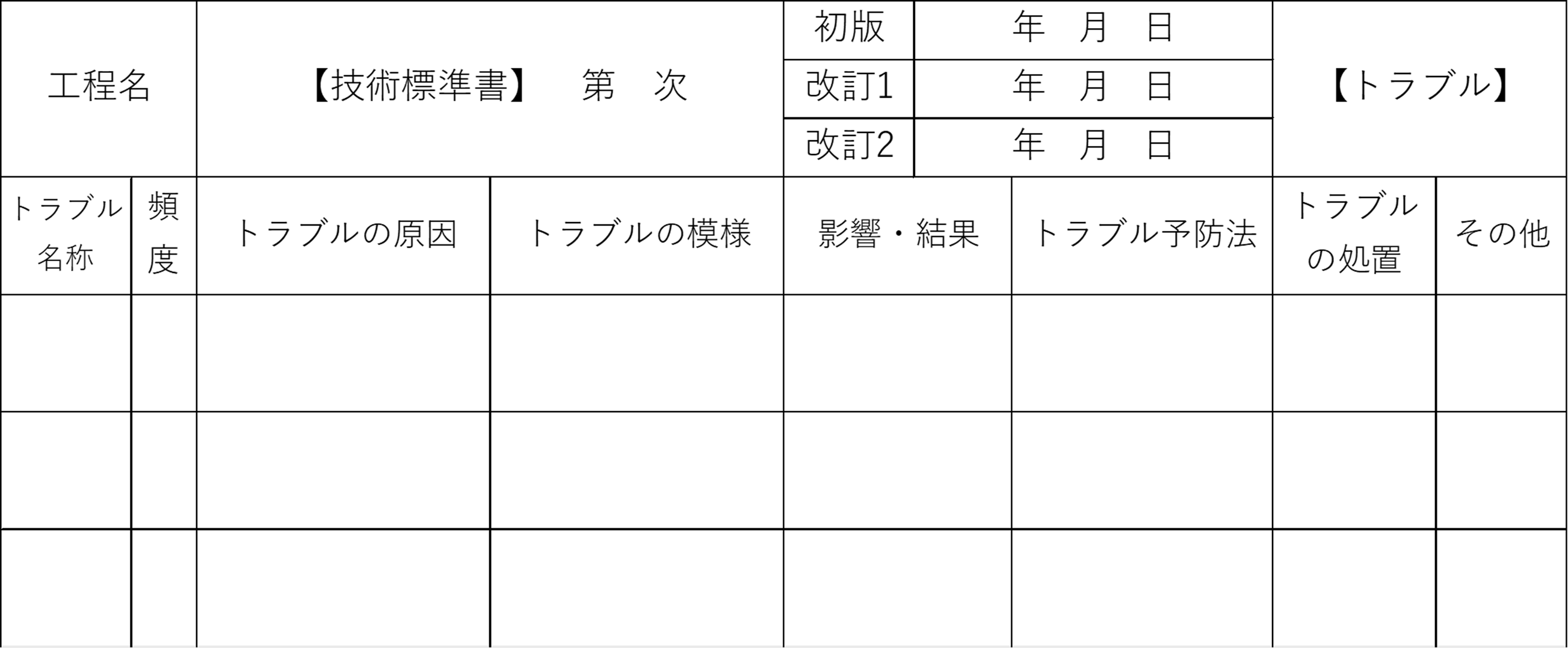
これらの要素は独立して存在するものではなく、相互に関連があるため、それぞれについて調整し、1つの体系としてまとめることが重要である。当然、関連するフローシート、P&IDなどの技術資料にも改善案を網羅することを考えながら進める必要がある。
ここで、このような改善を進める上で、現状の生産設備の果たす機能と、能力をどこで止めるか、将来の拡張性をどこまで見込んでおくか、確認すべき基本的事項を次に列挙する。
① 生産品種、品目の変化に伴う柔軟性と対応可能範囲
② 生産能力(量、限界、余裕度等)
③ 生産性のリードタイム(生産速度)と想定できる稼働率
④ ユーティリティの余裕度
⑤ 排水設備の能力と余裕度
⑥ 工場レイアウトと設備レイアウト / 機器配置
⑦ 設備の信頼性(個別機器、システム)と安全性(設備、作業)
⑧ 自動化および管理の対象範囲と内容(グレード、方式等)
⑨
工場運営の組織と管理者、スタッフ、オペレータ個々の守備範囲、役割の明確化
などである。
この中で慎重を極めるのは、「設備レイアウト」と、「人」に関わる問題である。特に混合・包装型ラインの食品工場では、菌や異物混入などの衛生安全に伴う衛生環境に重点を置く必要があるため、既存工場では建物、設備レイアウトを変更することは容易にできないし、影響度が大きい。また自動化の基本になる「流れをつくる」ことからも、FMS化を実現するためにも、設備レイアウトの決定は極めて重要になってくる。また人の問題としてFA化による個々のスタッフ、オペレータの守備範囲や役割も見直す必要があり、必要に応じて教育・育成を先行して行うことも重要である。
(3) 自動化の基本は効率的な設備レイアウト
FMS対応の柔軟かつ合理的な製造システムを確立するためには、個々の機械設備が必要な機能を具備していることであるが、それにも増して重要なことは、機能的な『工場レイアウト』を計画することで、生産効率はもとより、作業効率、作業安全、食品衛生といった観点からも生まれるメリットは大きく、十分時間をかけて検討しても引き合う。
レイアウト計画は、敷地、建物を含めた『工場の総合レイアウト』、生産効率を上げるための機械設備の配置を主にした『設備レイアウト』がある。これからの食品工場は『衛生第一』で、「みせられる工場」を基本に、鮮度、品質の確保が重点項目になってくる。これを達成するためには工場レイアウトが大きな課題で、しかも、その鍵を握っているといっても過言でない。
食品工場の総合レイアウトで考慮されるべき基本事項を列挙する。
① 目的や用途による製造現場区分の明確化
・汚染作業区(落下菌、カビ対策)と非汚染区の区分
・高湿区と乾燥区の区分
・製造場所の外部隔離(出入口の配慮 /
手洗い、着替え、下足替え、ヘアネット着用、
エアシャワー、ビニールカーテン、陽圧管理)
・汚染対策付き空調システム
・専用見学者通路の確保
など
② 貯留、保管の方法、適性場所の設定
・原材料、包材、仕掛品、製品などの貯留、保管
・保管条件 / 環境(常温、冷蔵、冷凍)
・形態(荷姿、量)
など
③ 機械設備の適性配置
・マテハンの容易なスペース確保
・搬送経路の確保(無人搬送車、コンベヤ、フォークリフトなどの配慮)
・段取り、段替え、洗浄時間の短縮
・有効作業スペース / 検査の効率向上、環境の確保
など
④ 機能的管理センターの配置
・試験、分析検査、
・コントロールタワー(管理・監視・操作)
など
⑤ ユーティリティ、サービスエリアとの有機的結合と有効な配置
・ボイラー、コンプレッサー、用水貯槽、変電所、排水処理施設の適性配置
・事務所、更衣室、休憩室、洗面所などの効果的配置
・廃棄物の一時保管
などである。
食品製造品固有の条件を満たしながら設備レイアウトを徹底的に追及、改善することである。特に混合・包装型ラインについては、次のことに着目し、改善を進める。
①
物の滞留、横持ちを少なくし、“物の流れをつくる”ことである。つまりバッチ、連続ラインを問わず、人と機械、機械と機械の連結とバランスを徹底的に追及する。
② 作業を平準化するための仕組みづくり。
③
短時間にしかも容易に型替え、段取り、洗浄などができるレイアウトを追及し、少ロット、多頻度生産を可能にする。
このようなことに着目し、改善を進めることによって自動化の基本である効率的なレイアウトを計画することができる。
(4) 作業の解析、改善に作業標準書を活用する
生産設備の自動化を行うためには、どうしても現状の作業を解析する必要がある。フローシート、P&ID、設備レイアウトといった各種技術資料を参考にしながら、作業標準書を作成してみることで課題や問題点が見えてくる。作業標準書は技術標準書の「作業」、「トラブル」よりも詳細に明記したもので、「作業手順書」、「作業指示書」、「故障早見表」、「故障処理手順書」の4つから構成している。ここですべてを作成することが理想ではあるが、「作業手順書」と「故障早見表」の作成を優先して作成し、後は適宜、作成することをアドバイスしている。場合によっては省略しても良い。
表5.~表8. に書式抜粋のサンプルを示す。
表5, 作業手順書の書式例
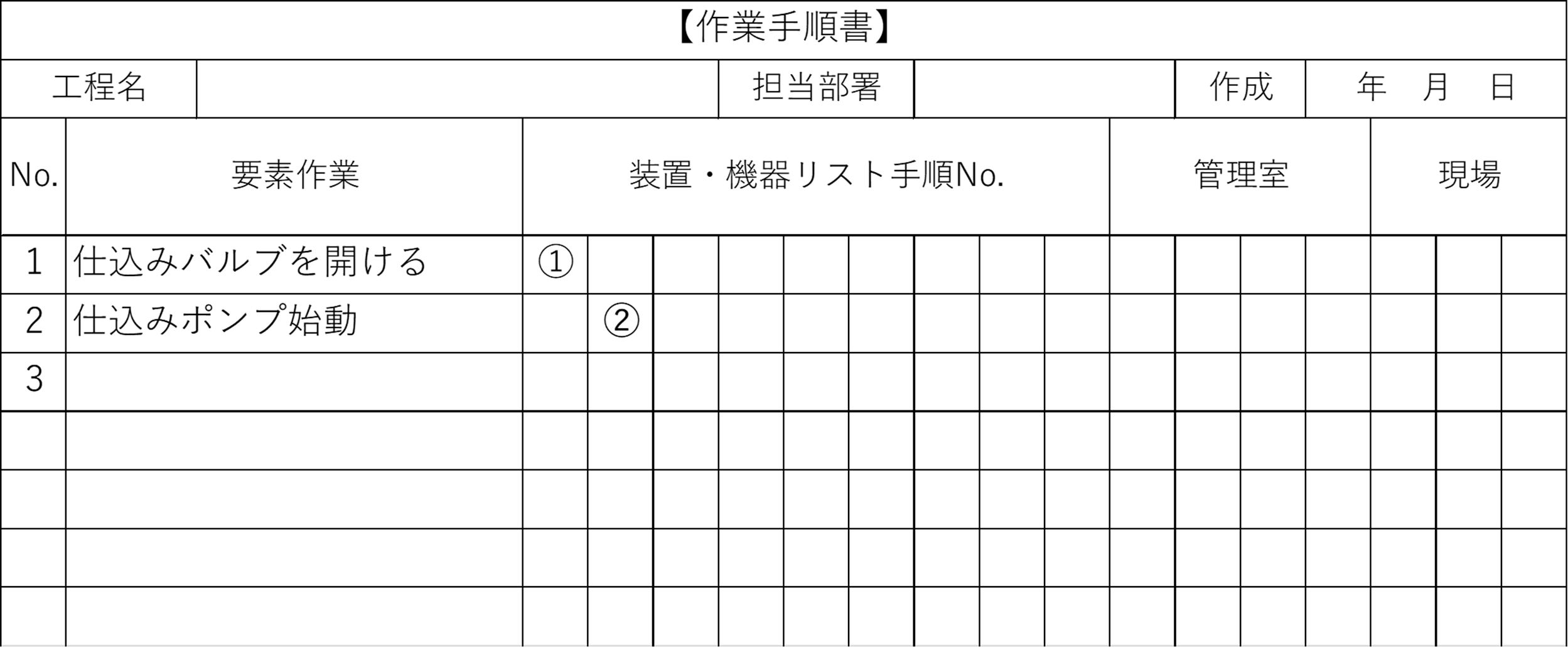
表6, 作業指示書の書式例
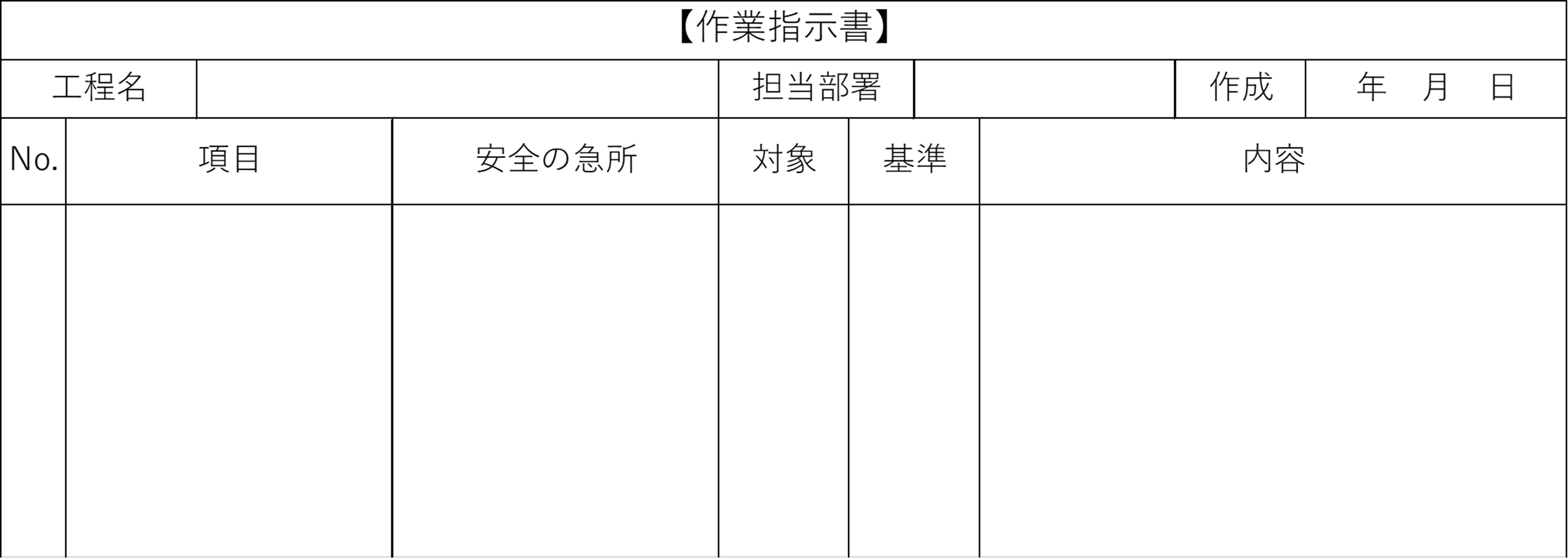
表7, 故障早見表の書式例
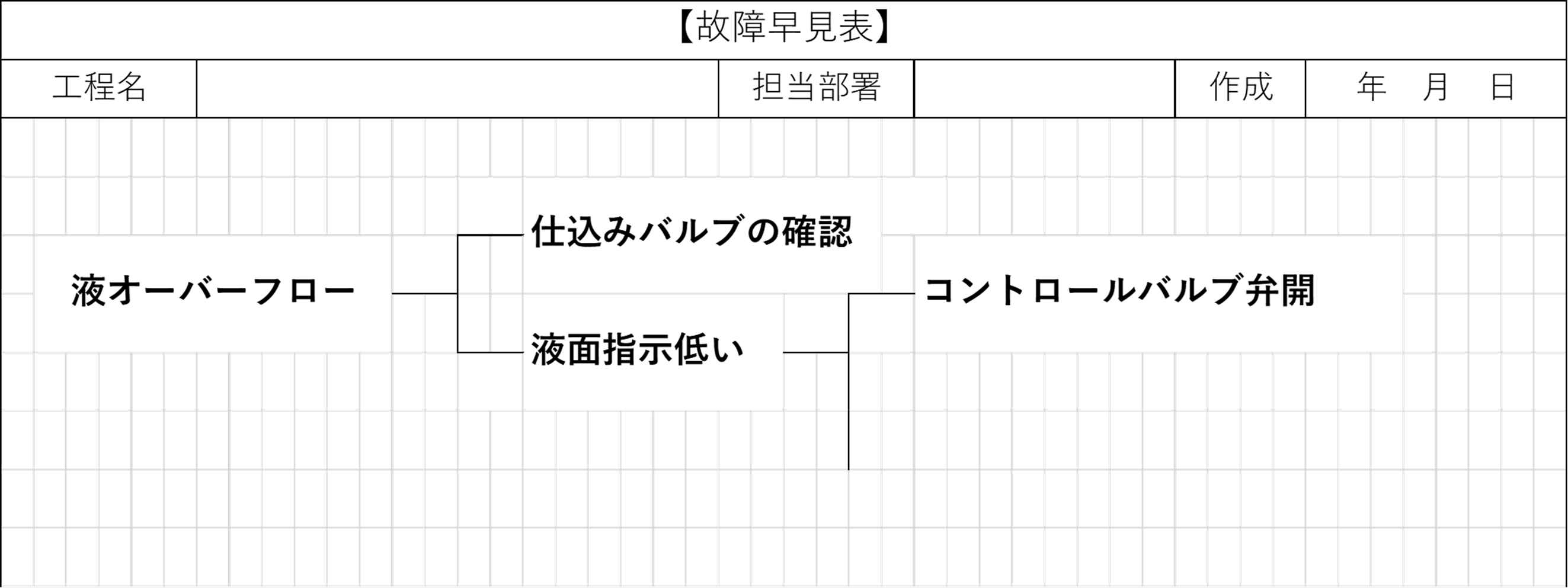
表8, 故障処置手順書の書式例
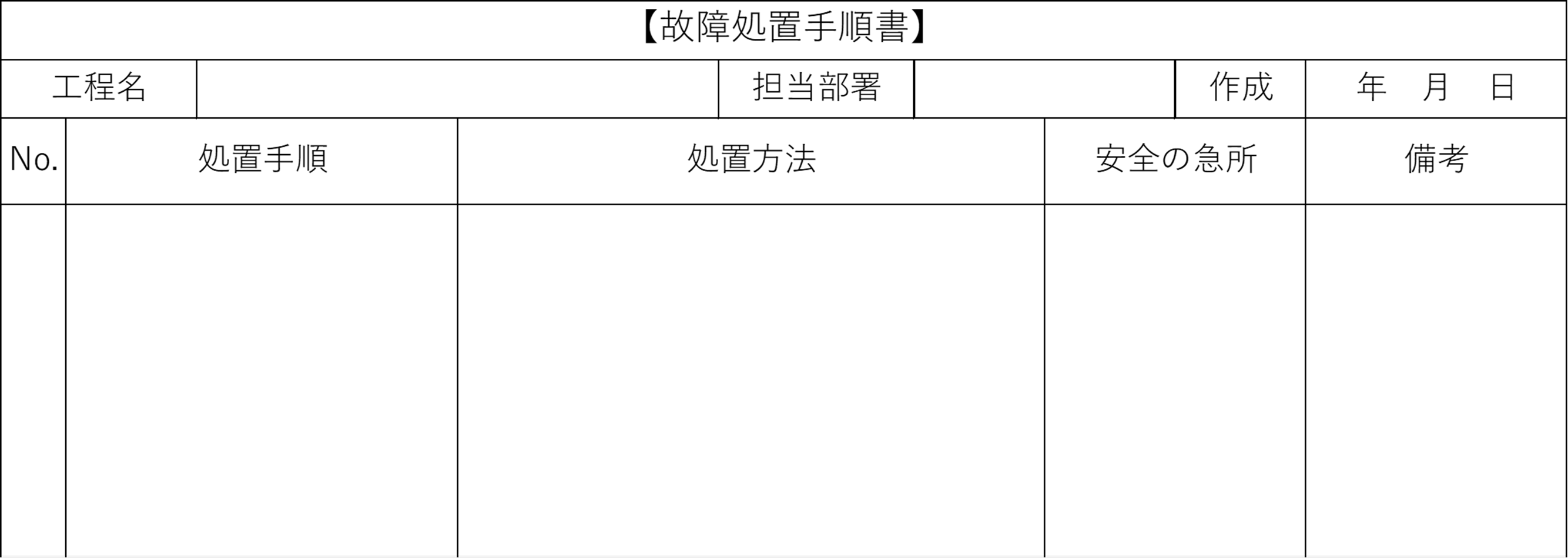
FA化が完了した時点で、できるだけこのような作業標準書を準備しておくことが望ましい。
(5) 自動化の糸口は作業測定とタスク編成
細分化された作業内容が明らかになり、トラブルの状況を掴んだところで、次に作業がどのような方法で行われているか、時間軸要素を入れ、定性的かつ定量的に作業を測定し、次のような非合理的な作業を洗い出す。
① 単純繰り返し作業
② 重量物を扱う作業
③ 悪環境での作業
④ 運動量の激しい作業
⑤ 作業を伴わない拘束されている(苦痛)作業
これらの作業から自動化の糸口を掴むことが重要である。
ここで、食品工場において簡易的な作業測定をする1つの方法について紹介する。その手順の概要を図4.
に示す。
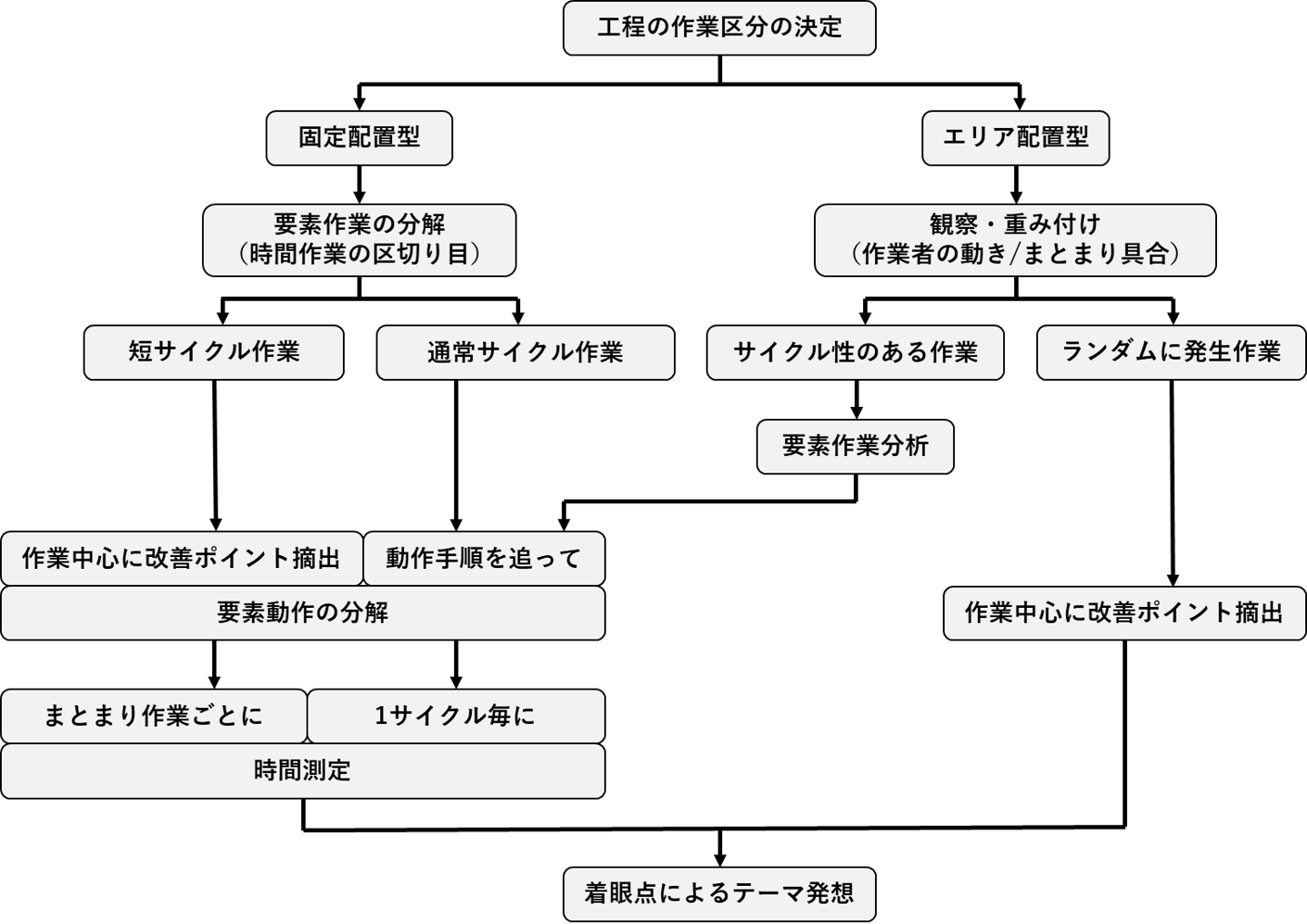
まず作業測定を行う前に、工程区分をはっきりさせて、作業測定の範囲を決める。工程とは、人の動きを中心に考えた作業の単位で、フローシートで使う工程とほぼ同じと考えて良い。例えば、受け入れ(払い出し)、計量(検査)、溶解(混合・撹拌)、ろ過、加熱(冷却)、分離、乾燥、分析、包装(荷造り)、ボイラー、用水(排水)などの作業となる。
食品工場の工程は千差万別といってよいが、大まかに分類すると定位置で作業する「固定配置型」と、比較的短時間に移動して作業する「エリア配置型」とがあり、それぞれ作業観測のアプローチ方法が変わってくる。
固定型の場合を例に説明すると、作業者が1度に遂行してしまう作業のまとまり具合(前後に休憩、待機が入っても良い)を時間測定の区切り目とし、それを1つの要素作業単位とする。分解した要素作業は、「短サイクル作業」と、「通常サイクル作業」に分け、前者は作業中心に改善ポイントを摘出し、後者は動作手順を追って、要素動作に分解する。この要素作業とは、作業を構成する人の動作のまとまりで、例えば、「pHを測定する」、「蒸気バルブで温度を調整する」などになる。このように要素動作を分解し、時間測定などを行い、着眼点を洗い出す。同様の方法を用いて「エリア配置型」も手順を追いながら作業を進めることが重要である。
このようにして得られた作業測定結果を図5.
に示すようなタスク編成表にまとめる。
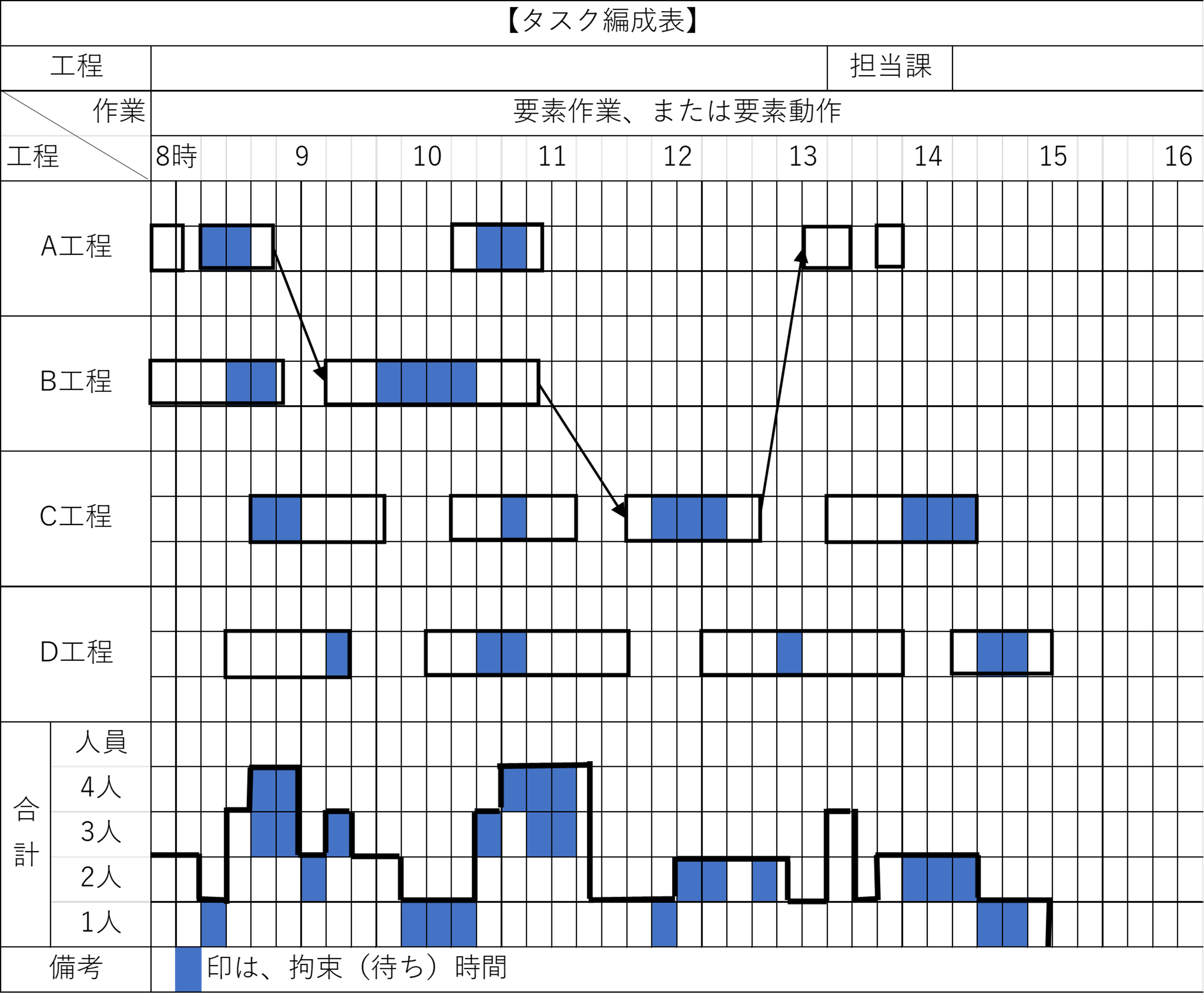
縦軸に工程、横軸に時間を取り要素動作または要素作業を記入すると視覚的に分かりやすい。各工程の要素作業を合計した山積み表を作成してみると、作業のピーク、余裕がはっきりしてくる。また作業はしていないが拘束されている時間を塗りつぶしてみると一層内容が明らかにすることができる。
作業測定方法は、作業改善の狙い目はどこかを見つけ出すことを目的としている。例えば、作業時間の変更は可能か、どこまで自動化が可能か、作業は簡素化できないか、できないとしたら代替えの方法はないか、などあらゆる角度から可能性を追求し、改善に結びつけることが大切である。
(6) プロセスの自動化と運転管理システムの着眼点
FAは「生産工場の管理を含めた自動化」を実現することによって、多品種少量生産に対応した新しいシステムを構築することである。ここまでは設備、人という観点から述べてきたが、「製造プロセスの自動化」と、「運転管理システム」の改善の着眼点を考える上で参考となる技術レポートを以下に明記する。
① 技術レポート『食品工場における自動化 (FA化) に向けた考え方』2023/05/22
https://www.kimoto-proeng.com/report/3440
② 技術レポート『食品製造プロセスの自動化アプローチ』2023/06/05
https://www.kimoto-proeng.com/report/3517
企業全体から見た生産システムは、OA領域に相当する経営管理システム、営業(販売)、経理(財務)、人事といった「情報処理システム」、さらにはFA領域に相当し、生産システムを統括管理する「生産管理システム」、直接運転に関わり、製造プロセスの運転操作、監視、管理を司る「運転管理システム」、直接運転を制御し、運転情報を収集する「製造システム」など、階層構造の総合体系から成り立っている。
5.活動フェーズⅢ:基本構想の立案・決定
フェーズⅡで、FAの対象工程をあらゆる視点から現状を把握し、解析、改善を進めてきている。このフェーズでは、数多く摘出された具体的な改善案を総合的に集約し、基本的な生産システムを構築することになる。その際、どこまで工場の「物の作り方」、「流し方」、「レイアウト」等を変え、それに自動化システムや管理システムを加え、期待効果に合わせたFMSを実現できるか判断しなければならない。ここでのFMSは合理化された柔軟性あるいは多様性のある加工システムで、理想的機能は次のようなものになる。
(1) 生産要求が変動した時、それに対して生産機能の変更が可能であること
(2) 生産機能の変更が自動化されていること
(3) 生産システムが省人化、無人化されていること、すなわち食品加工機械が自動化されていること
(4) 異なった生産機能を持つ食品加工機械1台あるいは複数台を併置し、生産要求に応じられること
(5) 所要の原材料が自動的に搬送、投入されること
(6) 原材料、中間製品が必要に応じて最小限ストックされていること
(7) 上記の機能が情報管理システムにより生産情報の授受によって、管理、制御されていること
ここで述べた7つの項目はあくまでも理想であるが、いかにこの理想に近づけるかが勝負である。物の流れの自動化と、情報の流れを体系的、かつ効果的に扱うことが重要になる。そしてこれを実現するためには、FAの要素技術を、手段として有効に活用できるように、フェーズⅡで得られた知見を基に手順を踏んで進めることが肝要である。
食品製造プロセスを大別すると次の4つになる。
(1) 原材料受入れ・保管
(2) 製造・加工
(3) 充填・包装・出荷
(4) ユーティリティ
この4つは相互に関係するが、内容が大きく異なるため、それぞれを区分して自動化および管理の対象を検討し、総合的な集約システムにすることが望ましい。図6.にFAのための工程、自動化、管理の対象例を示す。
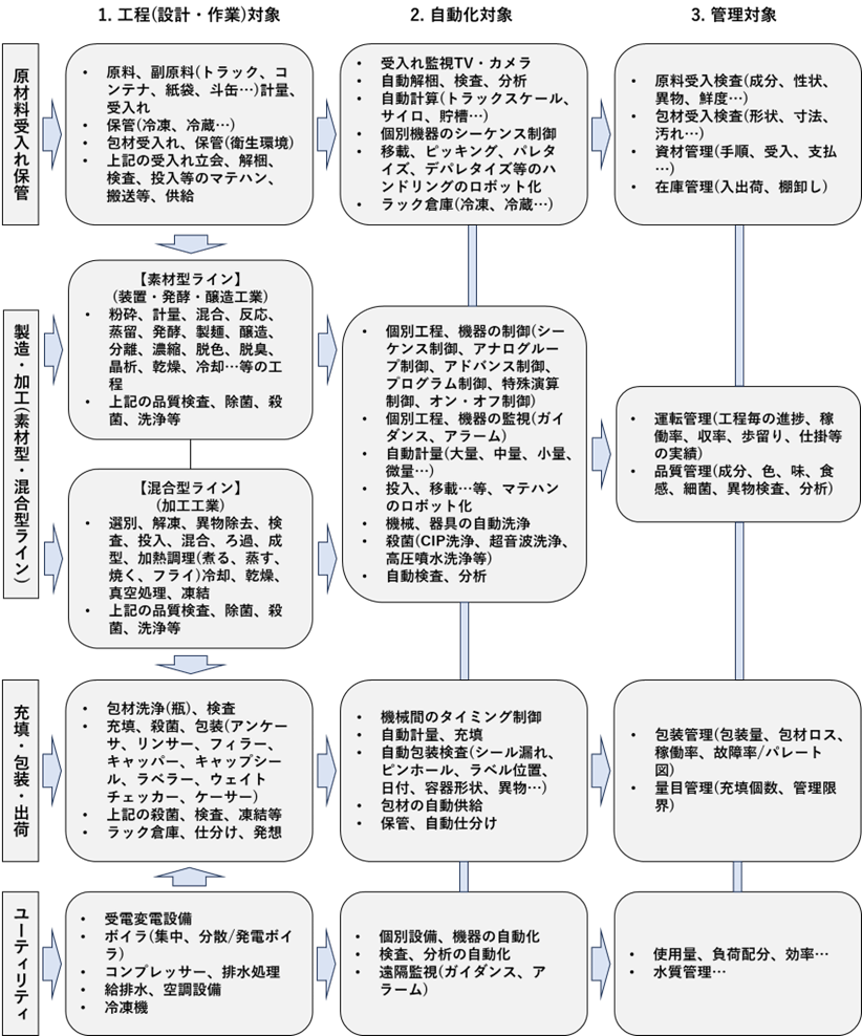
この4つを個々のブロックとして扱いフェーズⅡで作成した技術標準書、各種技術資料を基に結び付けると良い。基本的な構想を組み立てる場合、自動化および管理の内容と、FA化を実施する範囲を明確化し、工程別の構想を練り、全体の基本構想立案に落し込む。図7. 基本構想立案の検討項目を示す。
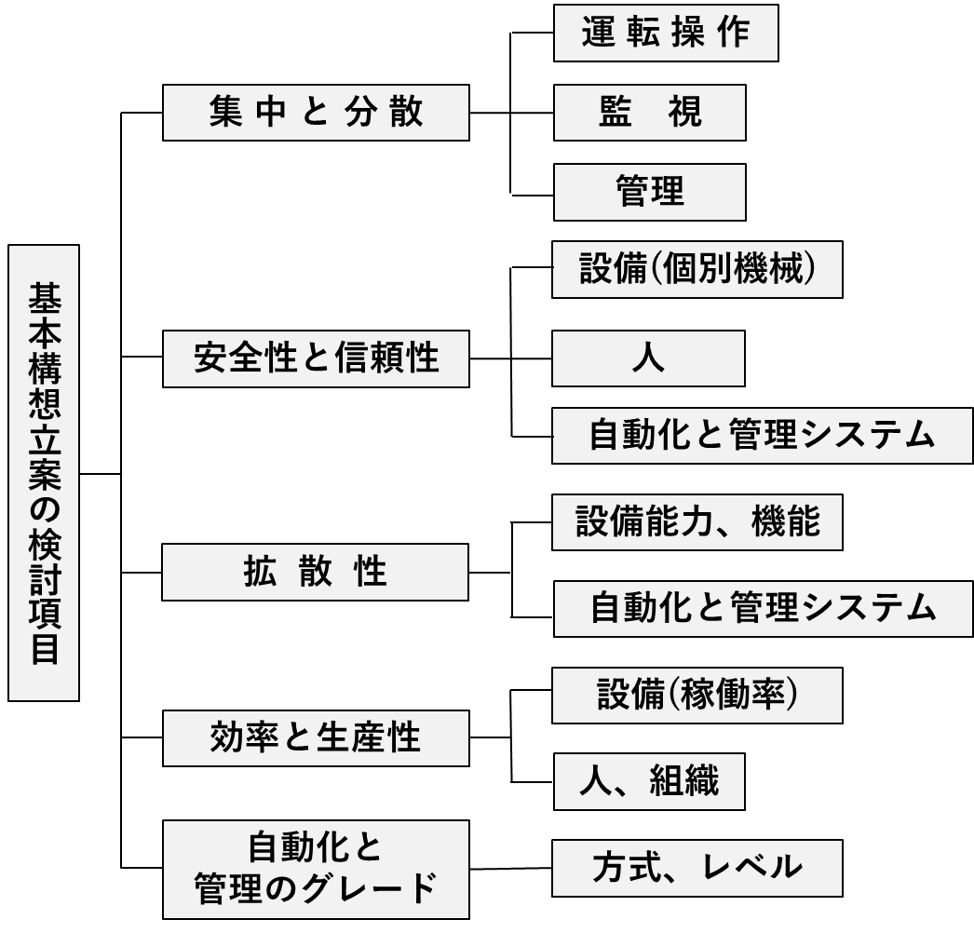
この系統図に示した5つの検討項目の基本的な考えをまとめ、これらの考えに基づいた基本方針を打ち出し、基本構想立案に反映させることである。
6.活動フェーズⅣ:具現化の検討
この段階になると、フェーズⅢで出来上がった基本構想を現実のものとして完成するために実行可能か、具体的な検討を進める。すなわち、基本構想立案時には、ある意味で仮定、仮設を立てていたものを確認しなければならない。そのためには、装置・機器のメーカーへ確認することや、調査のため出かけることも必要になってくる。さらに既存の製造方法の一部を変更する場合は、実験などによる検証・評価も行う必要がある。また新しい技術を採用しようとすると、自らの目で確かめることも大切である。
このフェーズで実施すべき具体的な項目を列挙する。
(1) 採用予定機器は、極力メーカーにおいて実機確認を行い、必要に応じてテストを依頼する。
(2) 作業改善によって摘出された、例えば、搬送機器、段取り用治工具、洗浄器具などの設計と採用試験による確認をする。
(3) 基本構想に基づいた作業の詳細解析と、最終要員配置の検討、を決定する。新しく出来上がった基本構想を基に、オペレータ1人ひとりの役割を決め、再配置し、計画初期に設定した要員と差異はないか、期待通りの成果が得られそうか、などについて最終の詰めを行う。特に導入する設備が高度化するためオペレータの教育訓練計画はもとより、スタッフの役割と人数についても併せて検討しなくてはならない。
(4) 予算のために必要な見積作業を行う。予算の精度を上げるには、詳細仕様まで決めて個々のメーカーに見積書を依頼するのが間違えないが、しかし、この段階での詳細仕様策定は困難である。ここでは、明らかになっている仕様の範囲でメーカーと相談して、予算を設定することである。まずは定価ベースで積算し、適宜修正して予算化することである。図9. に仕様書の種類、図10. に見積依頼書の記入項目を示す。
表9, 仕様書の種類
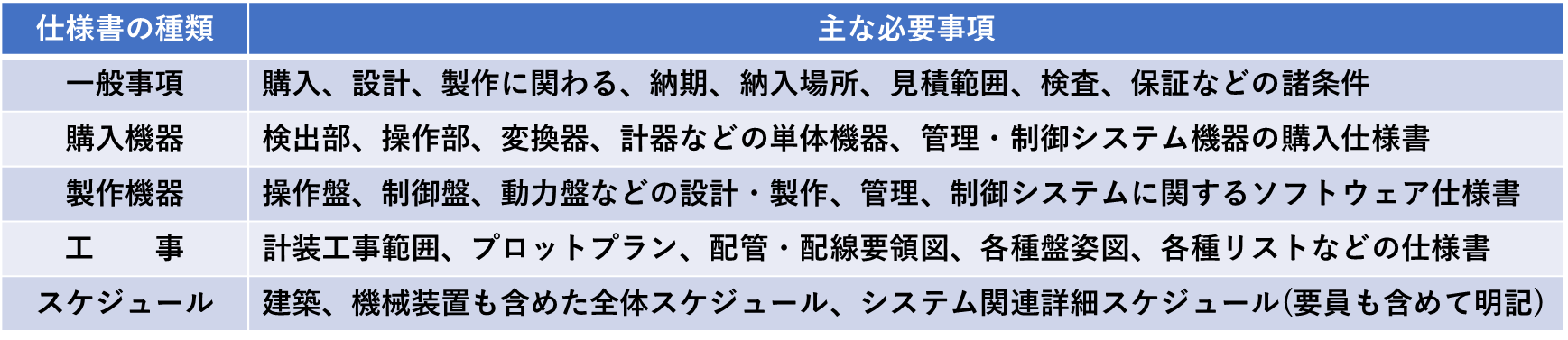
表10, 見積依頼書の記入項目
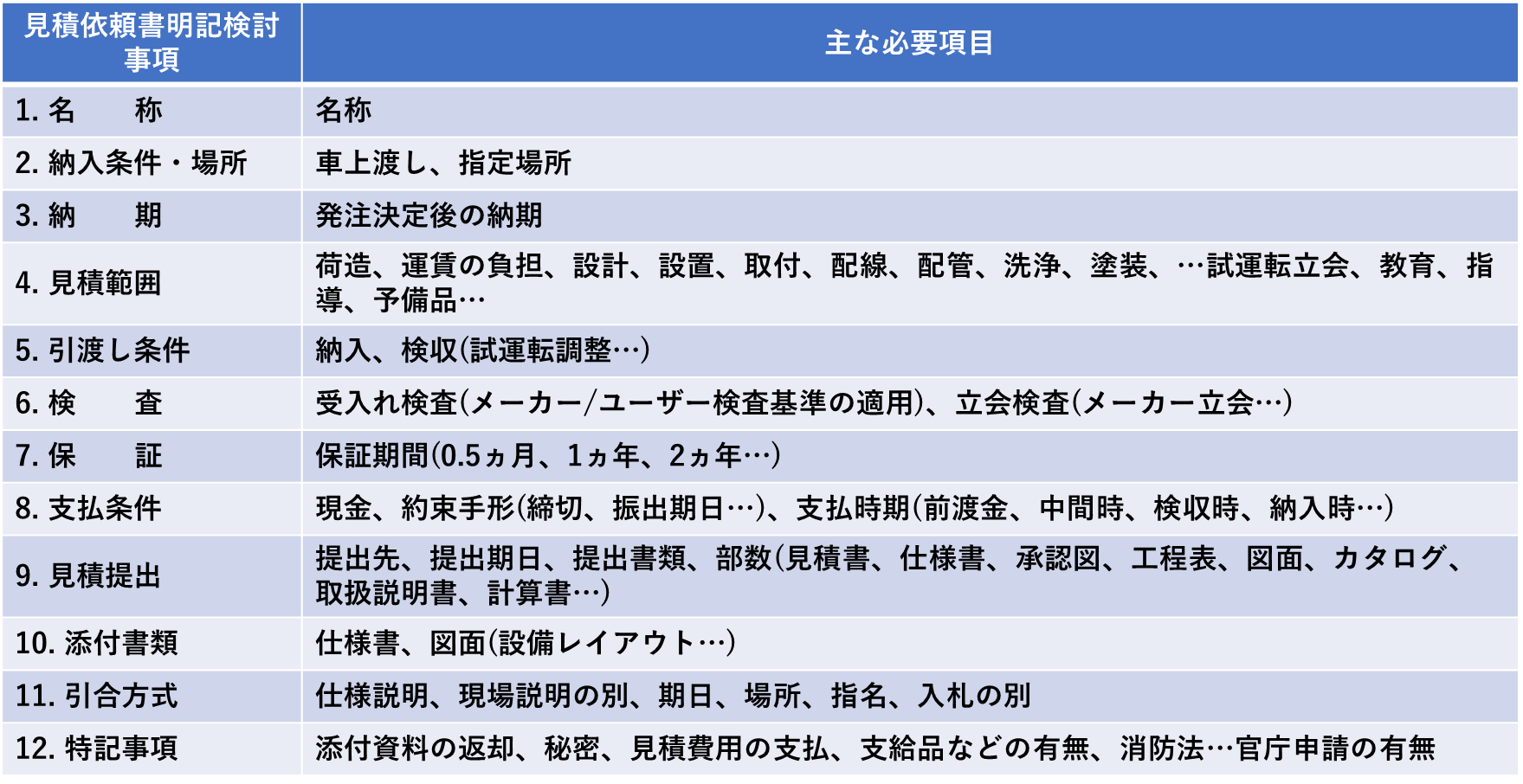
(5) 実施にあたって制約条件の整理と確認を行う。新しい基本構想の中で、物、人(組織)、金、それぞれの観点から制約されるものはいったい何か、もし制約されるものが出てきた場合は、どう除外できるか、など検討する。
(6) 実行スケジュールと、メンテナンスを含んだ推進体制の立案を行う。自動化に関連する部分だけでなく、実際は機械設備について詳しいものが必要である。それぞれの項目の作業を並行して実施することになるため、どこにネックがあるか、人員は十分か、などについて検討しておく必要がある。
7.活動フェーズⅤ:全体の統合化と経済性の検討
このフェーズは、これまで進めてきたプロジェクトチームの活動の総まとめとなる。フェーズⅣの具現化の検討で、実用上問題ないとされたものを、P&IDをはじめとする資料に反映させて、最終的に結合化することになる。プロジェクトチーム活動の答申書としてまとめ上げ、経営TOPの判断を仰ぐことになる。ここで大切なことは、プロジェクトチームがスタート時点で描いていた、FA化、新しい生産システムについて比較評価し、実現可能な答申となっていることが肝要である。
8.最後に
某企業の自動化設備導入計画の検討からスタートし、経営TOPに判断を仰ぐための答申書をまとめ上げる支援・アドバイスを行った事例から重要と考える取り組み方、進め方についてレポートとした。
秘密保持契約の関係で具体的な数字の提示や具体的に導入した装置・機器の情報、商品情報などフェーズごとに説明を割愛して明記している。
チーム活動の総括として、何が上手くできたのか、そして何が上手くできなかったのか、
次の活動にどのように活かすかなどと、それぞれのメンバー1人ひとりが別テーマでの推進リーダーとしてどのように関わっていくか、など反省会で意見交換を行って6ヶ月間の活動を完了した。
以上