2024/01/22
「食品用ミキサーの新規導入時のリスクアセスメント事例」
1.はじめに
食品工場における「リスクアセスメント教育・指導」を行った際の機械設備を新規に導入する場合に事前に実施すべきリスクアセスメントによるリスク低減方策の検討・適用と再評価、残留リスク対応までを行った事例として紹介する。
2.本コンサルの取組み方針
工場の設備診断によってリスク低減が必要と感じた工程の中で特に「食品用ミキサー」を題材にリスクアセスメントの教育・指導を実施することになった。本工場の社内規定および作業基準書などの整備を行うとともに、作業者が毎日の業務で取り扱っている機械設備の状況を正しく把握し、さまざまな作業行動に対して安全を確保できるように、現場の状況を「正しく認識し管理する」安全管理手法を構築することが、本コンサルのゴールである。
3.新規設備の導入および発注基準
安全管理基準のベースとなるプラント建設や生産ラインの設計では「設備安全基準ガイドライン」を活用し、取扱う原材料や製品から個々の工程、さらに全体のフローに対してもリスクアセスメントを実施することとした。
新規設備の導入時には「設備安全基準ガイドライン」に基づいて関係者全員によるリスクアセスメントを実施し、この「設備安全基準ガイドライン」は、安全、衛生、環境、品質の4つのキーワードで分類し、例えば安全では、「はさまれ」「巻込まれ」などの有無を確認すること、などの実施すべき事項を明記するものとした。
ただし、その場合において既存設備でのガイドライン資料においてはISO 14121の危険源リストは取り入れられていない。その理由は、新たに導入する機械設備は、新たな機能を持った設備というよりも、既設機械の置き換えや増設などを目的とする場合がほとんどであることから、ほぼ同等の形式の設備となる。したがって、危険の実態も既設機械とほぼ同じと考えてよいと判断できるからである。よって、新たな危険源が潜んでいる可能性も極めて低いので、ISO 14121の危険源リストを参照するまでもないと考えて差し支えない。
4.本工場の受入れ手順
工場が導入する機械の多くは既製品をベースとして、工場の製造品目、使用目的に合わせてこれに部分的な改造を施すのが一般的である。工場の関係部署と設備担当ならびに購入先メーカーとで機能的な改造や技術的な安全対策の検討および設計を行い、それに伴う改修を依頼する。
工場への受入れまでに安全管理部門、あるいは生産技術部門で設備改修内容の確認をして、工場設置後には、同じく担当部門で現場のリスクアセスメントを実施し、追加対策の有無を確認する。さらにリスクの再評価、最終確認を行い、最終的な安全確認を経て本格使用、生産作業に移行する手順とする。
5.実施内容の具体例
5-1.機械設備の概要
・名称:食品用ミキサー(ニーダータイプ)
・容量:300 L
・導入時期:2024年5月
・機械概要:以下説明
各種の原材料を混練り(あるいは混合・撹拌)槽内に投入し、加熱後、電動機で駆動される槽内の回転羽根で練り合わせる(混合・撹拌したりする)機械設備である。新規に導入するこの機械は、本工場の既設機械と異なり、混練り加工時に原材料を加圧しない構造となっている。
【補足説明】
ニーダー(kneader)とは
複数の原材料を撹拌・混合しながら練り上げる機械装置である。容器(混練り槽)を密閉して圧力をかけて練り上げる加圧式タイプと、常圧のままの容器槽内で練り上げる開口式タイプ(非加圧)とに分類される。
5-2.リスクアセスメントの実施手順
実施したリスクアセスメント手順の概要
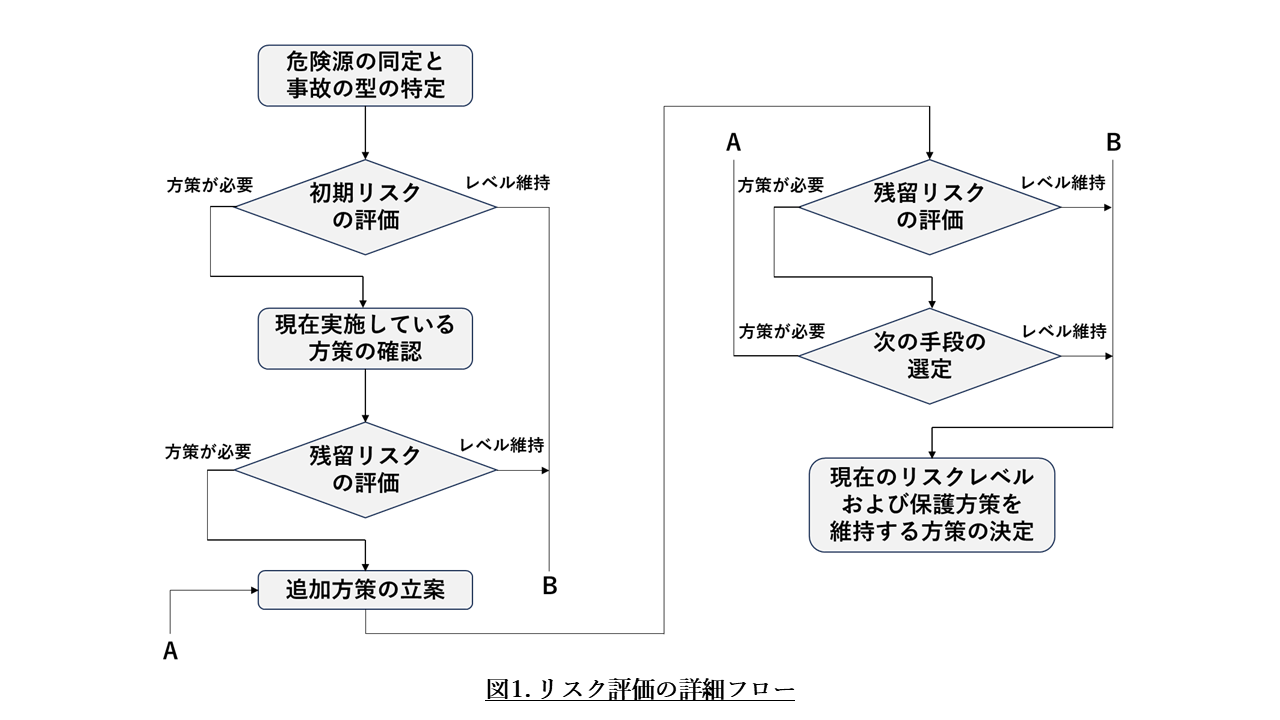
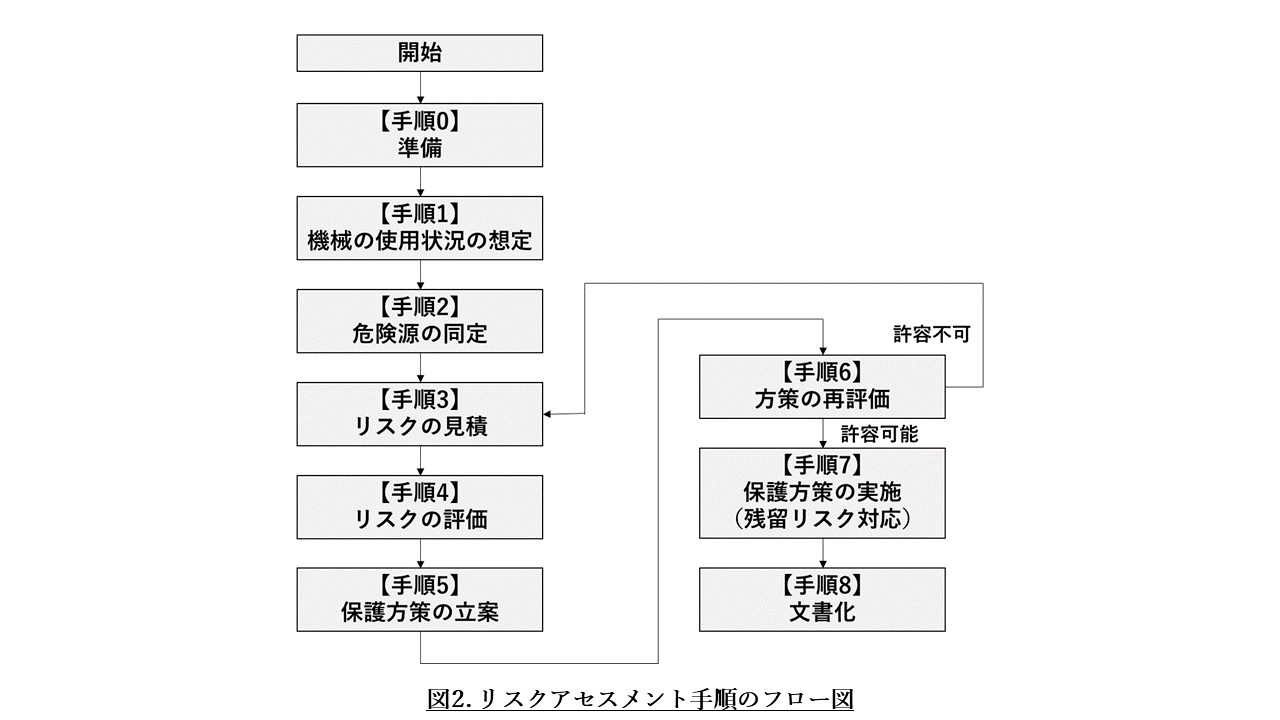
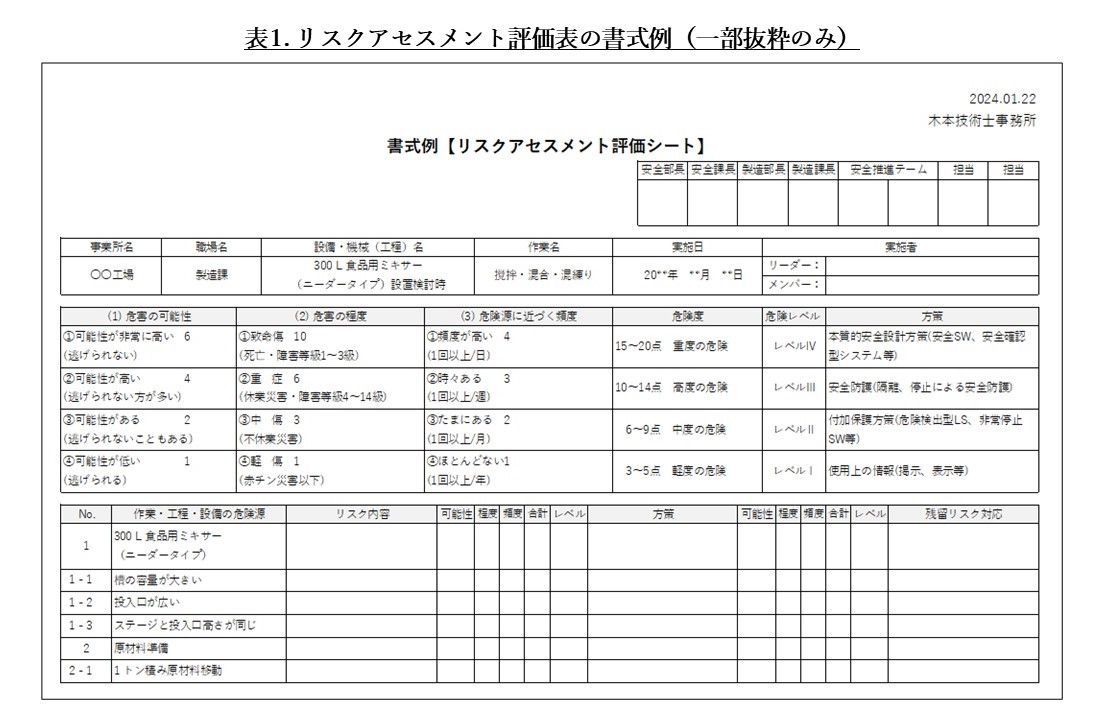
<リスクアセスメント実施記録の具体例>
【手順0】『リスクアセスメントの準備』
(1) リスクアセスメント実施者
・構成メンバー:6名
(内訳:生産技術担当者1名、現場作業者3名、安全衛生担当者1名、品質保証担当者1名)
(2) 対象機械設備の状態確認
・設計図面、設備仕様および詳細内容、製造工程図、設備現場の状況などの確認
(3) リスクアセスメントの実施時期
・新規導入時(設置検討段階)
(4 ) 機械メーカーからの残留リスク情報
・残留リスクに関する情報の入手状況
残留リスクに関する情報は、類似した既存の設備が工場にあるため、すでに保有していた。また、同種(オープンタイプ)設備をすでに導入している他工場およびメーカーからも関連情報を収集した。
なお、取引関係にある機械メーカーを概観すると、リスクアセスメント、機械安全設計原則、保護方策に関する知識が不足していること、また、ユーザーが設備の誤った使い方(予見可能な誤使用)をすることの想定および設備の使いやすさへの配慮が欠けていることが問題点としてあげられる。
【手順1】『機械の使用状況の想定』
(1) 機械メーカーからの残留リスク情報
・リスクアセスメント実施前の保護方策の状況
原材料(粉体)の仕込み中に槽蓋(金属製:ステンレス製)が落下する(自重で急激に閉じる)恐れ、仕込み中や清掃中に他の作業者が機械を起動して回転羽根が駆動される恐れなどがあった。両リスクとも安全対策が取られていない状況であった。また、仕込み量の増大や仕込み投入口の高さ不良(作業者が原材料を投入する際、不自然なかがむ姿勢で腰痛のリスクが大きい状態)であった。
(2) 使用状況の想定
使用状況の想定とした主な内容を項目ごとに一覧表で示す。
表2. 食品用ミキサー(横型開放ニーダー)の使用状況の想定
項目 | 内容 | |
---|---|---|
機械の用途 | 撹拌混合・混練り加工 | |
機械を使用する目的 | 食品原材料・調味液などをむらなく均一に混合し生産するための原材料の混練り加工 | |
稼働時間(時間帯) | 就業時間(8h)の内、通常4h運転 | |
予見される主な誤使用および機能不良 | ・仕込み・清掃作業中に、他の作業者等が誤って回転羽根の起動操作をする。 ・仕込み作業中に重い槽蓋が急激に閉じる (落下する)。 ・作業者がステージ(2 m)から床へ転落する。 ・作業者が仕込み口から槽内へ転落する。 |
|
主な仕様 | 製品型式 | 〇〇〇〇〇 省略 |
形 態 | 撹拌、混合、混練り機(単体機械) | |
容 量 | 300 L | |
主電動機 | 75 kW インバーターモーター | |
材料排出方式 | 電動反転式 | |
機械質量 | 約7,500 kg | |
危険対象 | 作業者(通常運転時) | オペレータ:1名 |
保全者(保守、必要時のみ) | 保全要員:2名 | |
その他 (接触が予見される人員) |
周囲の作業者:5名 |
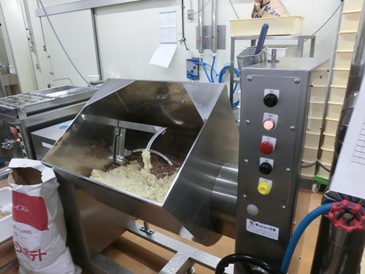
【手順2】危険源の同定
作業工程順に、JIS B 9702:2000(ISO14121:1999 JIS)「機械類の安全性 – リスクアセスメントの原則」の附属書 A「危険源、危険状態及び危険事象の例」を参考にして危険源を同定する。
表1. 「リスクアセスメント評価表」に明記されたリスクアセスメント実施の対象(作業、工程、設備)は表3. に示す順にリスクアセスメントをするようになっている。
表3.危険源同定の手順
No. | リスクアセスメントの実施対象 |
---|---|
1 | 設備仕様(300 L 投入口開放ニーダー) |
2 | 原材料準備(原材料容器、袋) |
3 | 仕込み作業(原材料容器、袋の開封、原材料の槽への投入) |
4 | 撹拌、混合、混練り作業 |
5 | 取出し作業 |
6 | 清掃・修理作業 |
7 | その他 |
【手順3】リスクの見積
表1. 「リスクアセスメント評価表」に明記された各作業・工程・設備の危険源およびリスク内容(危険状態)ごとに、次のリスク要素について各区分に当てはめて、対応する点数を定める(表4.から表6.に示す)。この点数を計算式(式1)に当てはめてリスク見積点数を算出する。
〈リスク要素と区分および点数〉
(1) 危害の可能性
表4. 危険源の可能性区分に対する点数
区分 | 点数 |
---|---|
① 可能性が非常に高い(逃げられない) | 6 |
② 可能性が高い(逃げられない方が多い) | 4 |
③ 可能性がある(逃げられないこともある) | 2 |
④ 可能性が低い(逃げられない) | 1 |
(2) 危害の程度
表5. 危害の程度区分に対する点数
区分 | 点数 |
---|---|
① 致命傷(死亡・障害等級1 ~ 3級) | 10 |
② 重 傷(休業災害:障害等級4 ~ 14級) | 6 |
③ 中 傷(不休業災害) | 3 |
④ 軽 傷(赤チン災害以下) | 1 |
【補足】
障害等級とは
業務や通勤が原因で負傷し、または疾病にかかり、その傷病が治っても身体等に後遺障害が残った場合における、その障害の程度を表わす指標のことである。国はこの障害等級を認定し、労災保険で程度(等級)に応じた障害補償給付を行う。この認定基準としては、障害等級認定基準が設けられている。
(3) 危険源に近づく頻度
表6. 危険源に近づく頻度区分に対する点数
区分 | 点数 |
---|---|
① 頻度が高い(1回以上 / 日) | 4 |
② 時々ある(1回以上 / 週) | 3 |
③ たまにある(1回以上 / 月) | 2 |
④ ほとんどない(1回以上 / 年) | 1 |
(4) リスクの見積の計算式
見積対象とするリスクについて、各リスク要素のどの区分に該当するかを想定し、それぞれに定められている点数を(式1)加算式によって算出し、合計点を基にリスクを見積る。
【リスク】=[危害の可能性]+[危害の程度]+[危険源に近づく頻度]…(式1)
【手順4】リスク評価
見積ったリスクの点数により、危険源の区分とそれに対応するリスクレベル(リスクの大小)を定める(表7. に示す)。
表7. 危険度の区分に対するリスクレベル
リスク | 危険度の区分 | リスクレベル |
---|---|---|
15 ~ 20点 | 重度の危険 | レベルⅣ |
10 ~ 14点 | 高度の危険 | レベルⅢ |
6 ~ 9点 | 中度の危険 | レベルⅡ |
3 ~ 5点 | 軽度の危険 | レベルⅠ |
【手順5】保護方策の立案
ISO12100 – 1(基本用語、方法論)、– 2(技術原則):2003とJIS B9700 – 1、– 2:2004の規格に基づいて保護方策を決める。リスクレベルに対応して、次の4つの保護方策を表8. に従って決定する。(食品ミキサーの設置図、外形図については秘密保持により省略)
表8. リスクレベルに対する保護方策
リスクレベル | 対応する保護方策 |
---|---|
レベルⅣ | 本質的な安全設計(安全確認型システム等) |
レベルⅢ | 安全保護(隔離、停止による安全防護) |
レベルⅡ | 付加保護方策(危険検出型のリミットスイッチ、非常停止ボタン等) |
レベルⅠ | 使用上の情報(リスク情報の開示・表示等) |
【補足】
安全確認型とは
安全装置の働きにおいて、機械の危険部分に人が近づいていないなど、センサー等で安全が確認できたときだけその機械の運転を許可する信号を発する方式である。
一方、危険検出型とは
安全装置の働きにおいて、機械の危険部分に人が近づくなど、危険な状態を検出したとき、その機械の運転を停止させる信号を発する方式である。
【補足】
安全確認型と危険検出型の動作の違いは何か
安全確認型の故障であっても、センサーの不具合で安全であることを検出できなくなったり、各部の配線が単線するなどで運転許可信号が送出できなくなることが考えられるが、たとえそのときが安全な状態であっても機械の運転はできなくなる動作をする。
一方、危険検出型の安全装置が故障した場合には、危険な状態を察知できなくなったり、検知してもそれを停止信号として送出できなくなったりして、危険状態が発生しても機械を止めることができない。すなわち災害発生を阻止する動作ができなくなるということである。
「人はミスをする、機械は故障する」とよく言われるが、安全装置も故障するものと考えなければならない。安全装置が故障したときには、この両リスクの保護方策の動作が人の安全を大きく左右することになる。
本ミキサーにおいては、原材料を投入する投入開口部の入口を高くする、槽蓋落下防止のロックシリンダを取付けるなど、リスクアセスメントの実施に基づいた保護方策を立案した。
【手順6】リスク低減の方策の再評価
立案した方策が妥当であるか、リスク低減策の内容について再評価を行う。すなわち、立案した保護方策を機械に装備した状態で、「危険の可能性」、「危害の程度」、「危険源に近づく頻度」の3つの要素を改めて見積、リスクレベルを算出してリスクの再評価を行う。
最初に立案した方策で必ずしもリスクレベルが適切に下がるとは言えないので、その場合は可能な限りリスクレベルⅠになるように【手順3】から【手順6】までを繰り返す。この繰り返しの中では、保護方策の立案【手順5】に最も注力することになる。そして、その結果少なくともリスクレベルがⅡ以下になることを確認する。
【手順7】残留リスク対応
リスクレベルがⅠまたはⅡまで下がったものの、上位3種類の保護方策(本質的な安全設計、安全防護、付加保護方策)だけでは適切なレベルまで低減できないと考えられるリスクが残っている場合がある。これを残留リスクと呼び、これに対する措置を表1.[リスクアセスメント評価表]に明記したように決定する。この措置は、作業管理、安全教育といった人的対策レベルでの方策となるのが一般的である。
これらの情報の現場作業者への周知は、次の3つの方法で実施する。
(1) 情報の発信者は、現場責任者(リーダー)が担当する。
(2) 現場作業者を含め現場関係者全員に、講義での教育、その後現場での指導・訓練を行う。そのときに、関係者で気づいた事項は、作業標準や作業マニュアルに追加する。
(3) 周知の回数は、少なくとも半年に1回以上実施する。
【手順8】文書化
(1) 定型の書式を作成、明記する項目は、(表1.「リスクアセスメント評価表」参照)。
(2) 文書作成時期はリスクアセスメント実施日の当日と決定する。
【補足】
文書化は、結果を記録として残すことだけが目的ではない。後で誰でも見直したときに、なぜこのような結果になったのかといった背景や原因がわかるようにしておくと良い。後で役立つ文書とすることが大切である。
総括
6-1.問題点の内容
取引関係にある機械メーカーは、既設設備の機械と同レベルの保護方策仕様となっていることからコンセンサス不足と判断し改善の必要を感じた。
6-2.改善策
機械メーカーと導入工場担当者間で保護方策について協議し、場合によってはメーカーを指導する形で、相互のコンセンサスを取りながら保護方策を決める。
6-3.今後の進め方
機械メーカー、導入工場のそれぞれの担当者において、再度ISO12100の安全規格と厚生労働省の「機械の包括的な安全基準に関する指針」の理解と周知を図りながら、機械設備の安全化に取り組むように提言書にまとめ提出し完了とした。
まとめ
「食品用ミキサー」を題材にリスクアセスメントの教育・指導を実施した。本工場の社内規定および作業基準書などの整備を行うとともに、作業者が毎日の業務で取り扱っている機械設備の状況を正しく把握し、さまざまな作業行動に対して安全を確保できるように現場の状況を「正しく認識し管理する」安全管理手法を構築することができた。
今後は、定着化に向けた個々の作業者の教育と訓練を定期的に実施することをお願いして本コンサルを完了した取組み事例である。
以上